高级会员
已认证
印刷油墨是由颜料或染料制成,这些材料赋予油墨以颜色,颜料是不溶的着色微粒,其粒径通常在微米范围内,分为有机或无机颜料。无机颜料通常用于制备非彩色油墨,有机颜料用来制备彩色墨水。
染料是非常小的颗粒(小于1纳米),通常可溶于介质中。它们因其着色力强和明亮的色调而受到赞赏,但在光照下,染料比颜料褪色快得多对颜料粒度的测量,能够很好的预测最终产品的性能。人们通常认为色强差、色差等问题是由于原料质量差造成的。事实上,这些问题是由颗粒粒径分布决定的。絮凝、着色强度、透明度、黏度和稳定性等因素均取决于粒径大小,因此这些问题可以通过优化粒径范围而得到解决。
为了证明黏度对粒径计算的重要性,我们使用Anton Paar Lovis 2000 ME粘度计测量了样品的黏度,并评估了该参数对DLS结果的影响。Lovis 2000 ME是一个滚动球粘度计,它测量了一个球在充满样品的毛细管中的运行时间。运行时间结合球和样本的密度可计算得到样品的黏度值。为了在一次测量中同时测量密度和黏度,Lovis 2000 ME与DMA™5000 M密度计同时耦合使用。
实验装置
样品为一种分散于甲基乙基酮(MEK)的白色二氧化钛颜料。样品原液浓度为1% v/v,实验中,原液使用MEK进一步稀释至0.5%和0.05 % v/v。
采用Litesizer™500进行DLS测量,温度设置为25°C,测试重复4次。因油墨浊度很高,测量角度手动设置为175°(背散射)。
黏度测量使用安东帕Lovis 2000 ME,仪器参数设置如表1。Lovis 2000 ME连接注射器,并设置为flow-through模式。每次测量后,依次使用MEK和乙醇冲洗,然后干燥。所有墨水样品的测量倾角均为30°。

结果与讨论
表2所示不同浓度下白色颜料的DLS测量结果。如图1所示,由Litesizer™500测得的透光率值可知,二氧化钛样品高度混浊。样品原液的透光率为0%,表明样品不透明。1/2和1/20稀释后的样品透光率分别为1%和52%(表2)。尽管如此,样品原液和1/20稀释后的样品水动力学直径结果差距不到7%。这证实了Litesizer™500在测量高浓度和浑浊样品方面的卓越性能,从而避免了对样品稀释的需要。
在第一组数据中,我们使用了溶剂 (MEK)的折射率和黏度来计算水动力学直径。然而,在高浓度样品中,分散的颗粒会对整个样品的黏度产生影响,进而影响DLS测量的准确性。
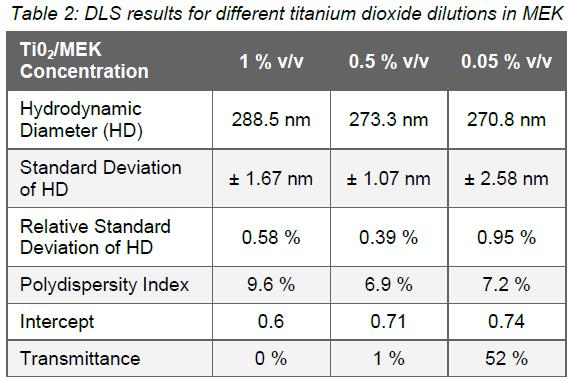
为了确定黏度对DLS结果的影响,我们使用Lovis 2000 ME测定样品的动态黏度。然后使用所得的动态黏度,重新计算我们之前的结果。
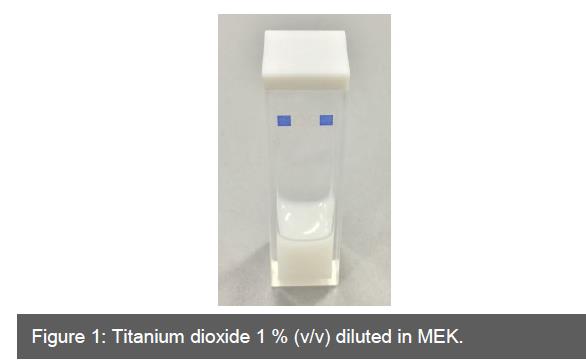
用Lovis 200 ME黏度计测得的密度、动态和运动黏度值如表3所示,采用测得的黏度重新计算的结果如表4所示。对两组数据的对比如图2所示。
两组数据结果非常相似。浓度最低的样品差异最大,其未校正值为271 nm,黏度校正值为246 nm,而这一差值不到10%。但需要注意的是,不同稀释度油墨样品之间的黏度差异不到3%(表3),这说明黏度的微小变化会对粒径产生成倍的影响。
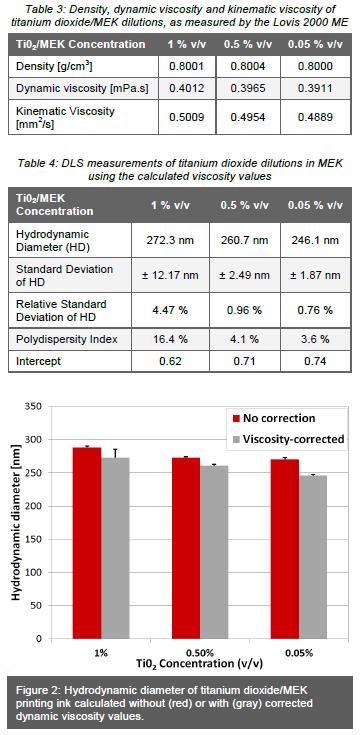
结论
通过实验,证明Litesizer™500可以在无需稀释的情况下测量高浓度油墨的粒径。我们比较了仅使用Litesizer™500获得的粒度数据,并将其与使用Lovis 2000 ME得到的粘度修正结果进行了比较。
两组数据之间的差异是有限的,在不同稀释度下,颗粒粒径的差异不到10%,相对标准偏差不超过5%。
一方面,这些数据证实了Litesizer™500背散射功能的有效性,该方法通过降低对多重光散射的敏感性来提高高浓度样品检测的有效性。
另一方面,此应用也证实了即使在样品准确粘度未知的情况下,Litesizer™500的粒径计算模型依然十分优异。但如果对偏差要求更高(小于10%),则需考虑样品的准确黏度,从而进一步提高测量精度。

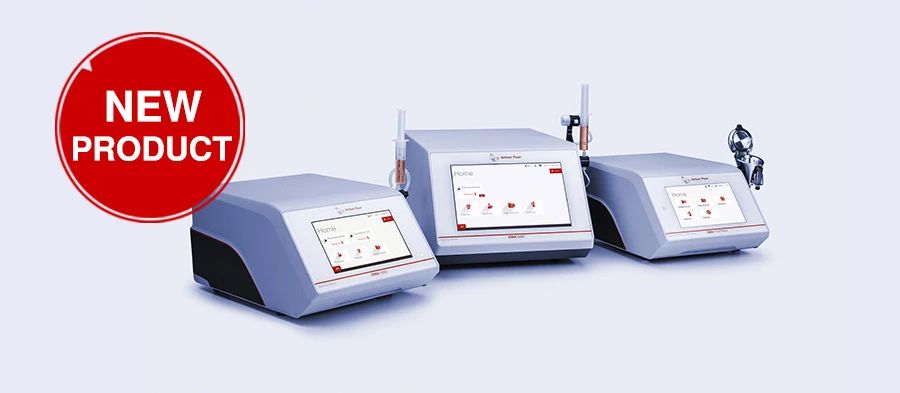
