金牌会员
已认证
锂离子电池作为一种有效的电能存储设备,具有能量密度高、比功率大、输出电压高、自放电小、使用寿命长等优点,目前已广泛应用于电动汽车、电子产品等领域。但其在电化学循环过程中,由于锂离子的脱嵌过程会导致电极材料的体积膨胀和收缩,且电池内部伴有产气、产热现象发生,均会导致电池整体发生变形,而这种形变尤以厚度方向为主。由于电池内部锂浓度分布不均,会导致电芯膨胀时的应力呈不均匀分布的现象。目前,针对锂离子电池应力的测量,一般只能测量电芯或模组的整体膨胀力,而少见测量电芯不同位置的膨胀力的分布情况。本文使用薄膜压力传感器实现原位监控电芯表面不同位置在充放电过程中的膨胀力变化。
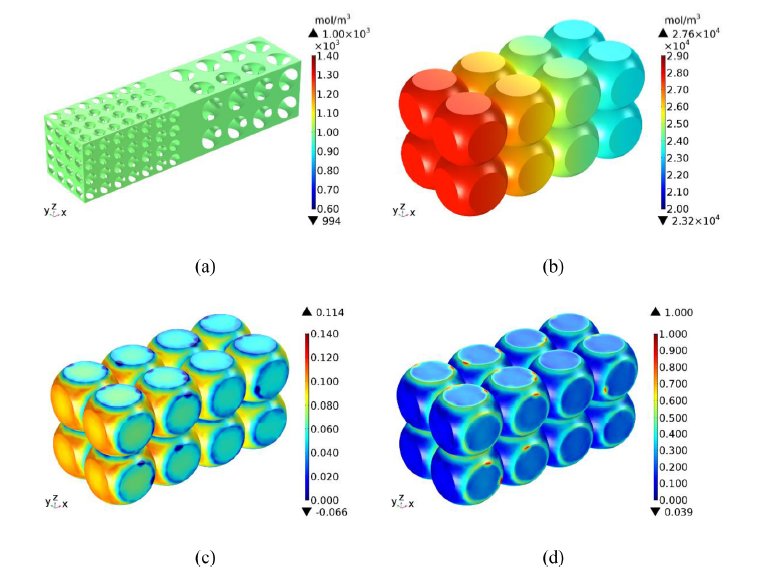
图1.锂离子电芯在满充时对应的锂浓度及应力应变分布模拟1
测试信息
· 测试设备:原位膨胀分析仪,型号SWE2110(IEST元能科技),可施加压力范围50~10000N,如图2所示。搭配压力分布薄膜(0~2MPa)测试电芯不同位置的膨胀力分布。

图2.原位膨胀分析仪示意图
· 测试参数:电芯信息如表1所示。
表1.电芯信息
· 测试流程:将电芯置于原位膨胀分析仪测试腔中,设置充放电参数:搁置60min,充电0.75C,截止电流0.05C,搁置10min, 放电0.75C,截止电压3.0V,同步开启原位膨胀分析仪实时监控电芯膨胀力变化曲线。
测试结果
对电芯在恒间隙模式下充放电三圈,同步采集电芯最大膨胀力曲线,如图3所示。随着锂离子不断从正极脱出并嵌入负极,导致负极结构膨胀,压力不断上升,充电结果峰值压力125.3kg。放电时锂离子从负极脱出回到正极,负极结构不断收缩,压力不断降低,放电结束时压力为56.9kg。如下图3所示。
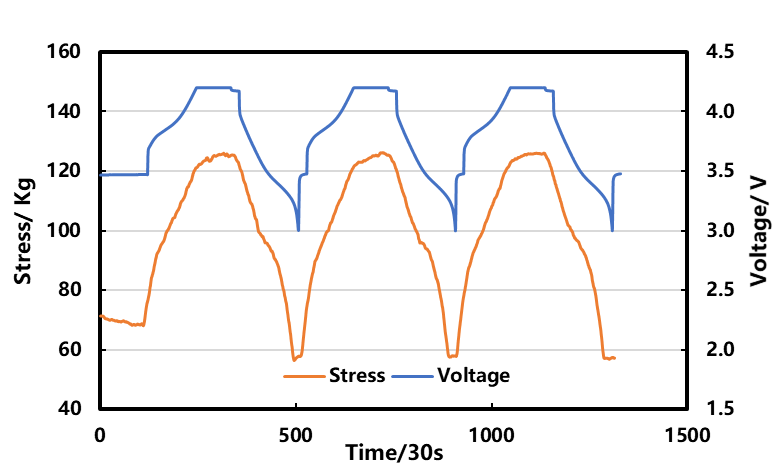
图3.电芯充放电电压和压力变化曲线
进一步分析电芯表面不同位置的膨胀力变化,我们把电芯划分为如图4所示的小单元,每一个小单元处对应一个压力传感器, 同步采集电芯充放电过程中每个位置的膨胀力变化曲线。
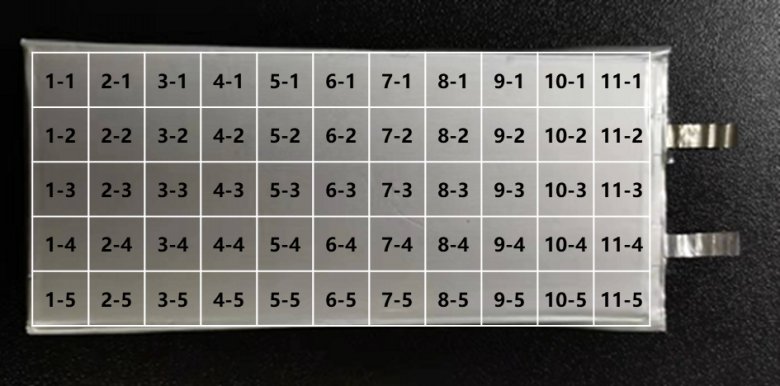
图4.电芯小单元区域划分
整个充放过程中各区域单元受力变化的热力图如图5所示,颜色越深代表膨胀力越大。随着SOC的增加,电芯中间区域的膨胀力可看到明显的增加,放电时,SOC逐渐降低,各区域对应的膨胀力又逐渐降低,总体变化趋势与图3一致,电芯应力呈现中间强四周弱,这可能与铝塑膜热封口边缘本身对电池有一定的限制作用,电池在充放电过程中边缘厚度膨胀比较小,另外还与卷绕电芯结构设计有关 ,同时膨胀力的变化也会受电芯收尾处贴胶以及极耳厚度影响。
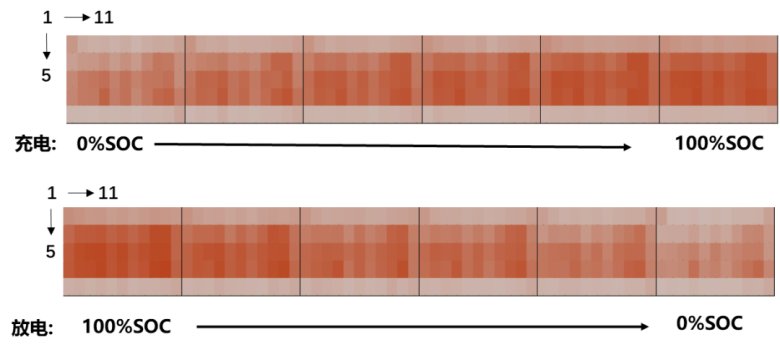
图5.电芯不同区域随SOC变化的热力图
对第二次循环充电的零电态和满电态对应的膨胀力分布进一步详细分析,如图6所示,虽然边缘处的初始膨胀力小于中间区域,但是满充后的膨胀变化率却是边缘处最大,这可能与卷绕电芯的拐角处更容易应力堆积或者析锂有关。
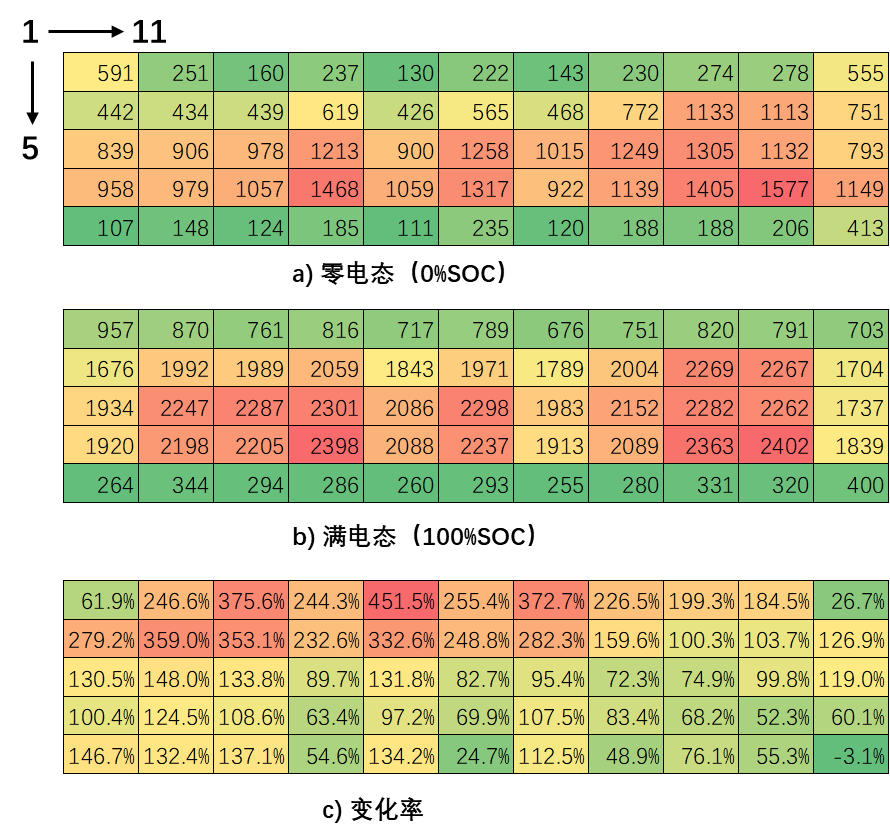
图6.零电态与满电态各区域小单元受力分布(相对值)
选取部分小区域单元膨胀力曲线如图7所示。从不同位置的膨胀力曲线的绝对值来看,边缘位置1、5、11处,膨胀力的绝对值是最小的,这可能与电芯初始表面不平,因此边缘处的初始受力更小,尤其是靠近极耳的位置11,基本上在充放电过程中也没有检测到明显的膨胀力变化,说明此位置基本没有接触到压力传感器。电池各区域应力分布不均匀可能还与卷芯内部的形变过程有关。在恒间隙模式下,充电时电池厚度膨胀,厚度膨胀对夹具形成作用力,夹具保持恒定间隙相当于对电池施加了一定的压力,在压力作用下,卷芯内部可能会发生褶皱和卷曲,如图8所示,导致各个区域受力不均匀。
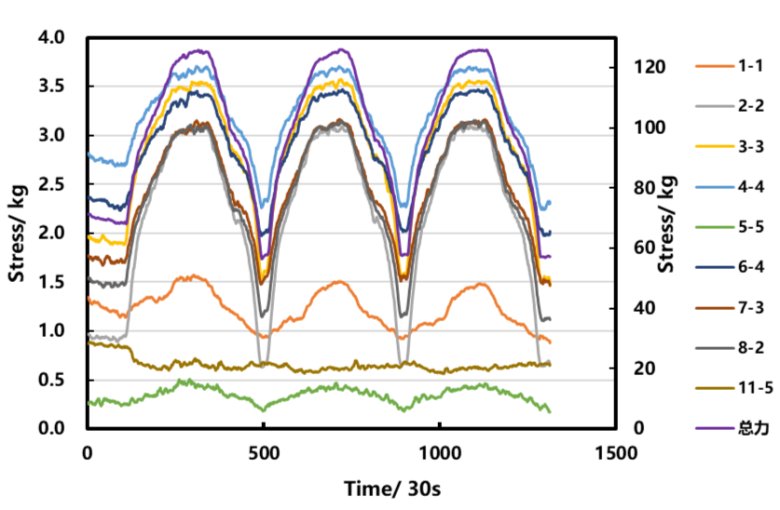
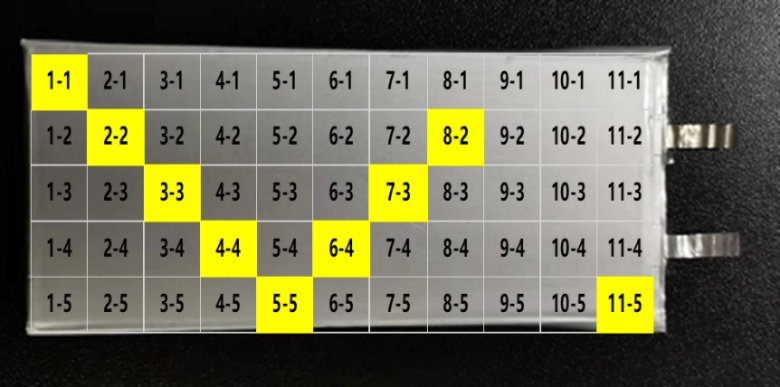
图7.部分区域小单元膨胀力变化曲线

图8.电池内部的形变过程示意图4
实验总结
本文采用原位膨胀分析仪(SWE)表征NCM体系电芯在充放电过程中的应力分布特征,进一步分析各小区域单元变化趋势,可定量表征出电芯表面的应力分布差异,为电芯应力分析提供更深层次的视角,可助力技术人员分析电芯内应力分布、探究失效电芯原因、开发更安全更可靠的电芯。
参考文献
1.Yanan Wang, Hua Li, Zhengkun Wang, Chen Lian, Zongfa Xie. Factors affecting stress in anode particles during charging process of lithium ion battery, Journal of Energy Storage, 43(2021)103214.
2.Anna Tomaszewska, Zhengyu Chu, Xuning Feng, et al. Lithium-ion battery fast charging: A review,eTransportation, 1 (2019) 100011.
3.Yongkun Li, Chuang Wei, Yumao Sheng, Feipeng Jiao, and Kai Wu. Swelling Force in Lithium-Ion Power Batteries,Ind. Eng.Chem. Res,2020, 59, 27, 12313–12318.
4.Ali M Y, Lai W J, Pan J. Computational models for simulations of lithium-ion battery cells under constrained compression tests, Journal of Power Sources, 2013, 242:325-340.
