金牌会员
已认证
锂离子电池是一个较为复杂的化学体系。随着近几年锂离子电池材料与制造工艺上的突破,锂电池被广泛应用到新能源汽车与大型电站储能领域。随着市场的逐步开拓,锂离子电池被应用到越来越多的场景,失效模式也越来越多。如何对电池的失效进行定量化分析,从而改善电芯是设计与制造工艺,无疑是研发与设计过程中非常重要的一部分。锂离子电池的失效分析是一个较为庞大的课题,涉及多个层级,包含了系统、结构、工艺、材料等多方面因素。
锂离子电池失效主要分为两种类型:一类为性能失效,另一类为安全性失效。性能失效包含了容量衰减、容量跳水、倍率性能异常、高低温性能异常、电芯一致性差等多方面。安全性失效指的是锂电池由于使用不当或者滥用,出现的具有一定安全风险的失效,主要有热失控、胀气、漏液、析锂、短路、膨胀形变等。这些失效可分解为下图[1]:
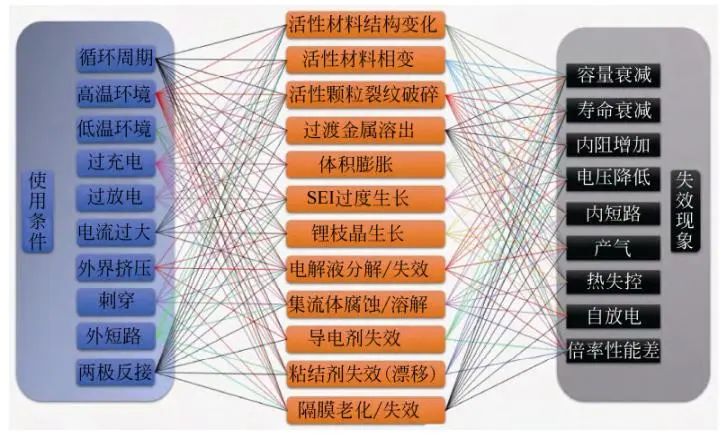
图1.锂离子电池使用条件、失效机制和失效现象的关系图
如图2所示[2],在电池失效特征分析-电池拆解样品制备/转移/表征一体化集成的系统分平台基础上,需要针对具体的失效现象,设计合适的失效分析方案,针对材料、极片、电芯层级分别选择上述的合适的分析检测技术,高效准确地获得电池的失效原因。同时还需将先进的测试表征及模拟仿真技术应用到失效分析中,尤其是原位表征、联用表征技术和装置。先进的原位表征技术有助于深入理解电池在实际使用条件下的反应机制、结构演化、界面演化等,避免电池拆解后测试分析过程对其实际状态的破坏。
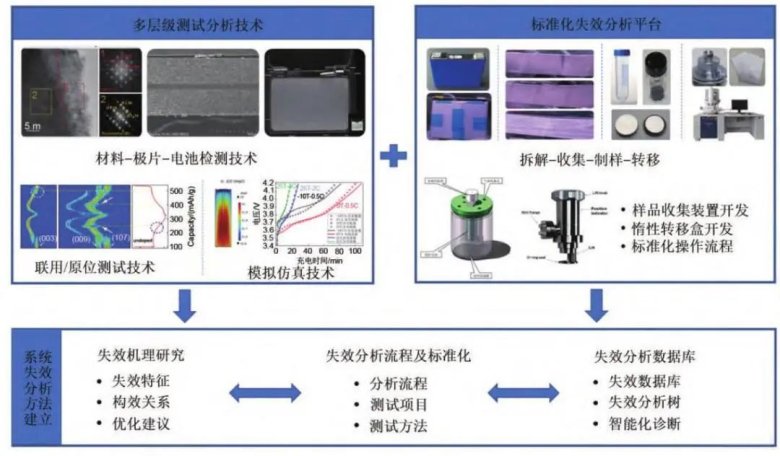
检测是失效分析的核心。元能科技是扎根于锂离子电池检测领域的检测仪器供应商,也希望在锂离子电池失效分析领域能够贡献自己的力量。为此,我们简单梳理了一下相关的失效分析流程,并结合元能科技自身仪器,做了一些相关应用。
失效分析的过程主要有如下几步:
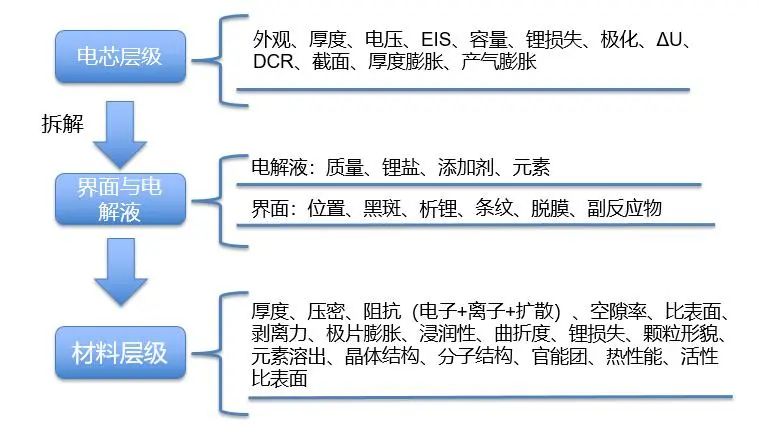
图3.失效分析过程图解
01电芯层级
在拆解电池前,我们通常会对失效的电池进行一些无损分析。主要步骤如下:
1. 调节SOC(100%SOC适合分析界面,0%SOC适合进行后期材料分析),拍照记录电芯外观,着重记录电芯破损、漏液、变形、产气等情况,测量电芯质量、厚度、电压等。
2. 剩余容量、DCR及EIS测试。将电池置于一定环境温度下,采用一定倍率进行0%~100%SOC充放电,检测电芯在一定倍率下剩余容量。如将电芯至于25℃常温环境,进行0.33C或者1C充放电,检测电芯失效后的剩余容量CEOL。调节到一定SOC后,可进行等相关测试。完成相关测试后进行全电池DCR和EIS测试,分析失效前后电芯内阻变化情况。
3. 电芯厚度或体积膨胀/收缩测试,采用元能科技原位膨胀测试仪与原位产气体积测试仪,可以同时进行失效后电芯充放电过程中的厚度变化与体积变化情况的研究,如图4所示。
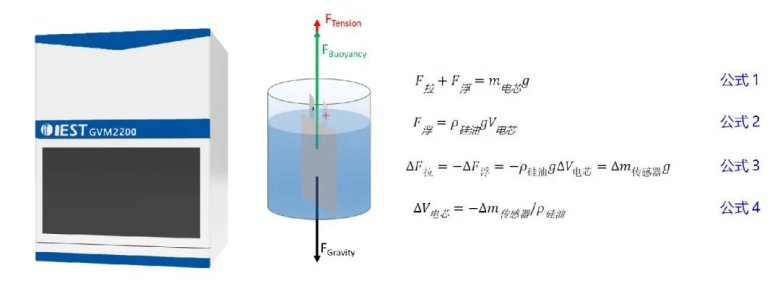
图4.元能科技GVM系列原位产气体积测试系统与原理
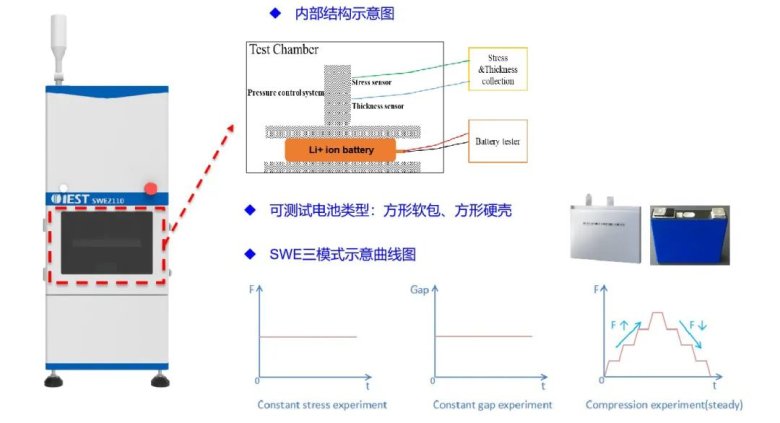
图5.元能科技原位SWE系列膨胀测试系统与原理
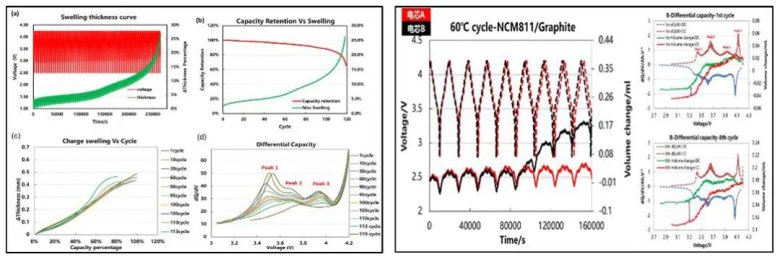
图6.应用案例:电芯中的循环膨胀与产气
4. 微分容量测试。采用低倍率(一般是0.04C)高频采点(1s)进行充放电。随后将充放电曲线制作成微分容量与微分电压曲线,即dQ/dV与dV/dQ曲线。结合步骤2和3,可通过曲线的峰移动位置与峰强度分析电芯极化、活性材料损失等相关变化情况[3]。
5. 断层扫描分析。完成以上相关测试后,可以对电芯进行断层扫描,获得电芯老化后的错位、形变、隔膜收缩等相关内部结构信息。
02界面与电解液分析
完成第一电芯层级的所有数据收集与分析后,开始对电芯进行拆解。拆解的电芯一般分为几种状态:100%SOC/50%SOC与0%SOC。100%SOC/50%SOC电芯可以用来观察明显的界面变化与阻抗变化情况,0%SOC电芯可以用来进行各项材料性能测试。主要过程如下:
1. 将产气后的电芯采用专用气袋进行气体收集,收集后进行GC测试,分析产气成分,了解电池在全寿命周期的产气量、产气成分及含量对于揭示电池的界面反应机理,提升电池安全性和循环寿命具有重要意义;
2. 拆解0%SOC电芯。拆解后完整的JR可以采用元能科技开发的电解液甩脱仪进行离心(图7),快速方便得到极片空隙中的电解液(该仪器支持280Ah大电芯进行离心),随后进行IC、GC-MS、ICP等测试,分析电解液消耗情况与元素含量。同时拍照记录极片界面情况,保留极片进行材料层级分析。
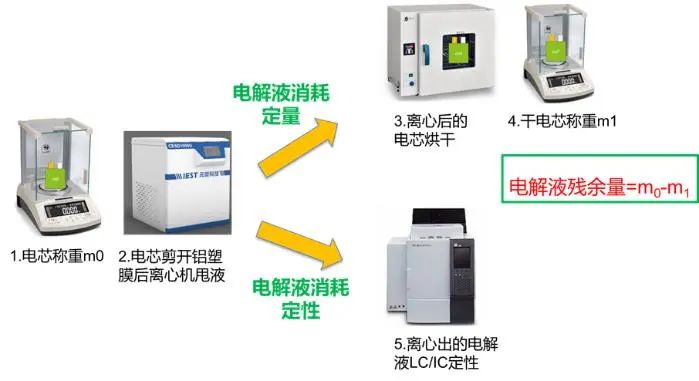
图7.电解液离心测试消耗量过程
3. 拆解100%SOC或50%SOC电芯。采用相机与万分尺等进行记录极片界面与厚度,包括界面、位置、黑斑、析锂、条纹、脱膜与副反应物界面与厚度情况。在这个过程中,我们应该重点关注极片表面是否析锂、极片的剥离强度情况、极片是否存在粉、金属杂质、毛刺等异物等。
析锂的表征既需要考虑电池使用过程中失效形式被触发的临界点及其演化过程的监测,还应该注重析锂量、锂沉积位置/形貌与电池整体安全性的多层级关联性研究。极片的剥离强度是评价极片机械稳定性的重要指标之一,常见的极片剥离强度下降表现有涂层从基材的剥离及涂层的开裂、局部脱落等,其致因因子大体分为活性材料脱嵌锂反复膨胀收缩、极片受热黏结剂失效和基材表面腐蚀等。异物可能会直接刺穿隔膜,也可能会在电池循环过程中溶解在电解液中后在负极表面析出形成金属枝晶刺穿隔膜,导致电池内部微短路,出现自放电。
03材料层级分析
在完成电解液与界面的所有数据收集后,开始材料层级分析。此时,不同的检测项目可以用不同的SOC的极片进行分析。不同的检测项目需要进行不同的前处理,部分电解液影响比较大的材料需要进行DMC浸泡清洗后再进行其他测试。材料层级的主要分析过程如下:
当拆解电芯为100%SOC时,进行部分界面与材料性能分析:
1. 对称电池阻抗分析与迂曲度分析。对称电池EIS可分析极片阻抗中欧姆阻抗、膜空隙结构阻抗、离子传输阻抗与扩散阻抗等。分析电池阻抗主要来源并进行分解,从而分析失效过程中的材料阻抗变化情况,分析电阻变化来源。在此过程中可采用元能科技多通道离子电导率测试仪,快速进行对称电池组装与测试,同时可进行极片迂曲度测试。
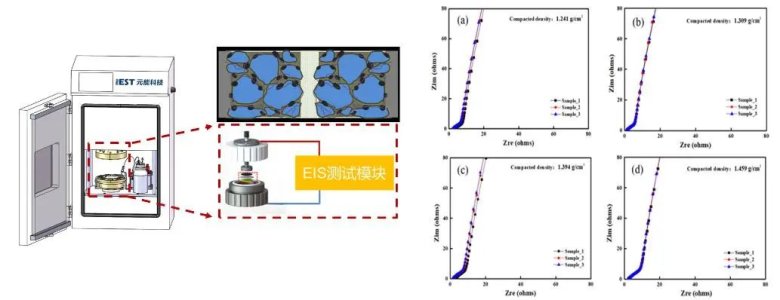
图8.元能科技多通道离子电导率测试系统与
不同辊压压密负极片对称电池的Nyquist图
2. 极片电子电阻测试。而采用元能科技BER系列极片电阻仪可快速进行极片电子电阻测试,分析电池组装增长来源。由于搭配了高精度的厚度传感器与压力传感器,可以实时测试极片压密与电阻变化规律。应用案例如图10中所示,黑色线为极片对称电池Rs值,蓝色线为极片电阻Re值,Rs与Re增长规律一致,但是在高温循环与高温存储中两者电阻增长来源不同,说明其失效模式不同。
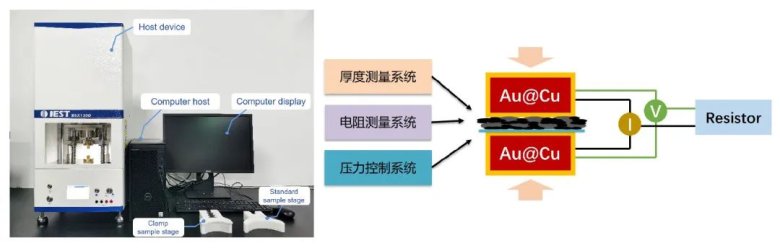
图9.极片电阻测试原理与BER系列仪器
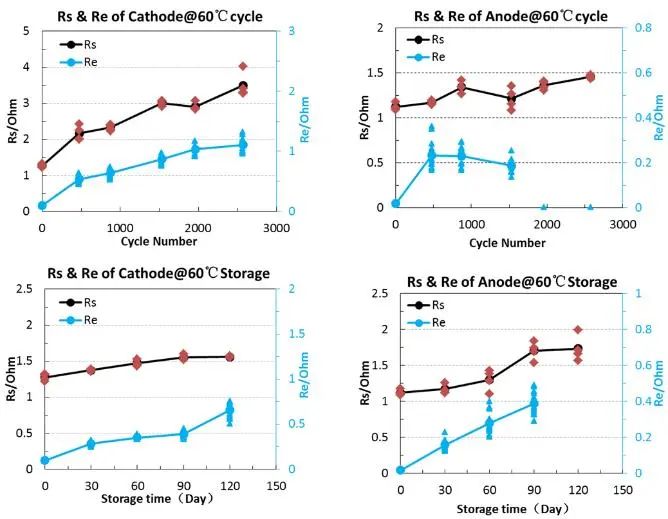
图10.高温循环与高温存储过程中的Rs与Re变化
3. 材料热稳定性分析。从满充后的正负极极片中刮下来粉末,采用TG-DSC等可进行材料热稳定性分析,对比失效前后的材料热稳定性变化,尤其正极材料。
当拆解电芯为0%SOC时,进行材料理化性能分析:
1. 容量分析。将极片擦单面后组装成反向扣电,进行克容量测试,从而分析材料的剩余容量与可逆容量,对比全电池dQ/dV曲线,可进行更加充分的锂损失与极化损失分析[4]。
2. 活性比表面。可以利用CV测试方法,进行材料活性比表面分析,从而对材料副反应进行侧面分析。
3. 孔隙率测试。孔隙率测试可以采用压汞法或者真密度法进行测试。由于汞为剧毒物质,目前行业上主要采用真密度法测试极片孔隙率。
4. 材料形貌与表面元素分析。可以CP-SEM-EDS进行观察极片及材料的形貌,包括膨胀、团聚、破碎、副反应堆积与相关形貌变化。同时结合EDS可以查看材料表面元素的变化情况,分析副反应物的产生等。如硅负极膨胀较大,不同工艺制备膨胀厚度不同,采用RSS膨胀测试与CP-SEM测试实际膨胀不同,如图12所示。
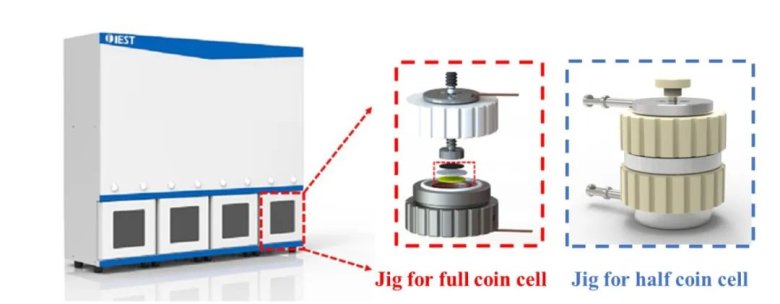
图11 扣电膨胀测试系统与硅负极膨胀快筛系统

图12.不同硅材料膨胀变化与实际极片厚度测试
5. 晶体结构与分子结构分析。采用XPS、NMR、CZE、Raman、XRD、TEM、TUNA、FITR、Raman等仪器,可以充分分析材料失效前后的晶体结构与表面分子结构变化情况,结合阻抗分析,可以更好的进行失效来源分析,从而对电池失效进行重点改善[4]。
6. 元素分析。采用ICP对正负极极片、隔膜与电解液进行元素分析,可以确定材料元素变化情况,尤其针对性的进行部分包覆元素与易析出元素分析可以快速确定材料包覆失效与元素溶出现象,针对性的进行改善。
04小结
锂离子电池作为多学科交叉融合的产物之一,其在现有社会生产与生活中都扮演了重要的角色,在未来的生活中也会扮演越来越重要的角色。针对电池的失效分析检测,越来越多的方法被开发出来,人们对电池的机理认识也更加深入。作为扎根于检测行业的年轻一员,元能科技希望能够通过新的检测技术,帮助行业人员更深入的认识材料与电芯,优化材料设计与工艺设计,提高产品一致性与可靠性,在失效分析技术上,做一份微薄的贡献。
05参考来源
1. 王其钰,王朔等,锂离子电池失效分析概述,储能科学与技术,2017,Vol5,No.15
2. 王怡,陈学兵,王愿习,等.储能锂离子电池多层级失效机理及分析技术综述[J].储能科学与技术, 2023, 12(7):2079-2094.
3. 堃博士,锂想生活公众号:锂离子电池拆解失效分析方法,2023-06-22
4. 方晨旭,长时储能电池性能失效机理研究,新材料应用与表征技术(厦门)交流会,2023
5. 魏丽英,锂离子电池关键材料失效分析,新材料应用与表征技术(厦门)交流会,2023
