金牌会员
已认证
随着制造业的快速发展和不断升级,航天航空、汽车等领域对产品的轻量化需求不断增加,同时也产品的性能、异形结构提出了更高的要求。在这些领域的大型产品制造过程中,最终部件或子组件的装配是一个不容忽视的重要环节。就飞机而言,在零件组装中一个零件的装配错误就会导致不良风险,甚至带来灭顶之灾。而利用传统制造技术进行生产,就需要付出大量的时间、设备、人力和质量控制,增加了制造成本负担,且不能满足所有复杂异形结构设计,具有很大的局限性。因此,企业需要一个高效、创新、满足复杂化设计需求的方法来减少工序环节,降低成本和避免风险,达到提质增效的目的。
当传统制造技术无法满足要求时,3D打印的集成化结构设计开辟了一条全新的道路,为3D打印技术释放了无限潜力。3D打印拥有无模化和对制造成本对设计的复杂性不敏感两大优势,可以将原本多个构件组合的零件化零为整,进行集成化打印,且无须任何机械加工或任何模具,这样不仅实现了零件的整体化结构,避免了原始多个零件组合时存在的连接结构(法兰、焊缝等),也可以帮助设计者突破束缚实现功能最优化设计,使企业能够更好更快地实现各类定制零件的生产制造。
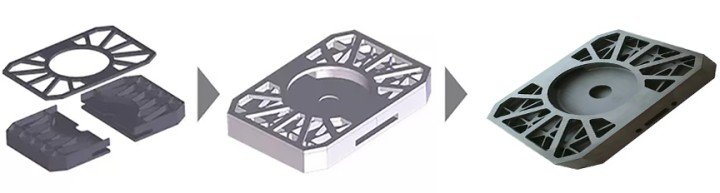
▲零件整合结构件(样品来源:升华三维)
而零件整合好处主要包括以下几点:
减少装配:这包括减少劳动力,库存,夹具/工具以及专用于最终产品的制造占地面积。装配检查也减少了,极大地减少了装配错误的机会。
减少故障点:长期降低维护成本,并且可以减少更换部件的库存。如果需要,可以快速且经济高效地进行小批量更换。
降低运营成本:由于增材制造,通过设计自由度优化零件,提高了产品性能,实现了零件轻量化和更好的热性能等增强功能。
例如火箭发动机的一体化喷注器的关键部件,喷注器由底座和喷嘴组合而成,原先采用传统的“机加喷嘴+分体焊接”制造方案,工序多、制造周期长。而且喷注器组成零件较多,焊接过程中,每条焊缝都有可能存在潜在的质量隐患和风险。但是利用3D打印技术,可以整体制造喷注器,一次打印成型,减少了部件数量及加工工序,大大缩短了制造周期,大幅提升了生产效率。由于少了中间的焊接工序环节,产品质量及可靠性也得到了提高。集成化结构的实现除了带来轻量化的优势,减少组装的需求也为企业提升生产效益打开了可行性空间。

如今,新一代战机、新型火箭发动机、火星探测器、汽车发动机等重点装备的关键核心零部件大量应用增材制造技术,解决了许多过去难以制造的复杂结构零件的成形问题,实现产品结构轻量化。升华三维是目前国内少数具备材料开发制备、3D打印机研发生产、切片软件开发到3D打印工艺、脱脂及烧结工艺一整套3D打印完整工艺链及解决方案的供应商。未来,升华三维将继续发挥自身优势,增强技术创新,努力践行“制造强国”战略,为建设“数字中国”添砖加瓦,贡献出自己的一份力量,推动我国制造业高端化智能化绿色化发展,促进实体经济和数字经济高质量融合。