白金会员
已认证
一、石墨电极:电弧炉炼钢关键耗材、原料成本占比达66.88%,超高功率化是发展方向
(一)材料定义:石墨电极是无定型碳经过石墨化炉焙烧制成的炭素制品
石墨电极是经过石墨化处理的炭素制品。根据我们在2017年6月26日发布的《炭素行业专题报告之一:钢铁用炭素(I)——新增电炉投放驱动石墨电极需求,技术进步、集中度提升助长期发展》,炭素制品按是否石墨化分,可以分为两大类,一是未经过石墨化处理、由非石墨质碳组成的炭制品;二是经过石墨化处理、由石墨质碳组成的石墨制品。
石墨化是指在高温电炉内把炭制品加热到2300 ℃以上,使无定形碳转化成具有三维有序的平面六角网格层状结构石墨的高温热处理过程。炭材料的石墨化是在2300~3000 ℃高温下进行的,由于化石燃料的燃烧难以获得如此高的温度,故在工业上只有通过电加热焙烧方式才能实现。通常采用石墨化炉,炉型有艾奇逊(Acheson)石墨化炉和内热串接(LWG)炉。
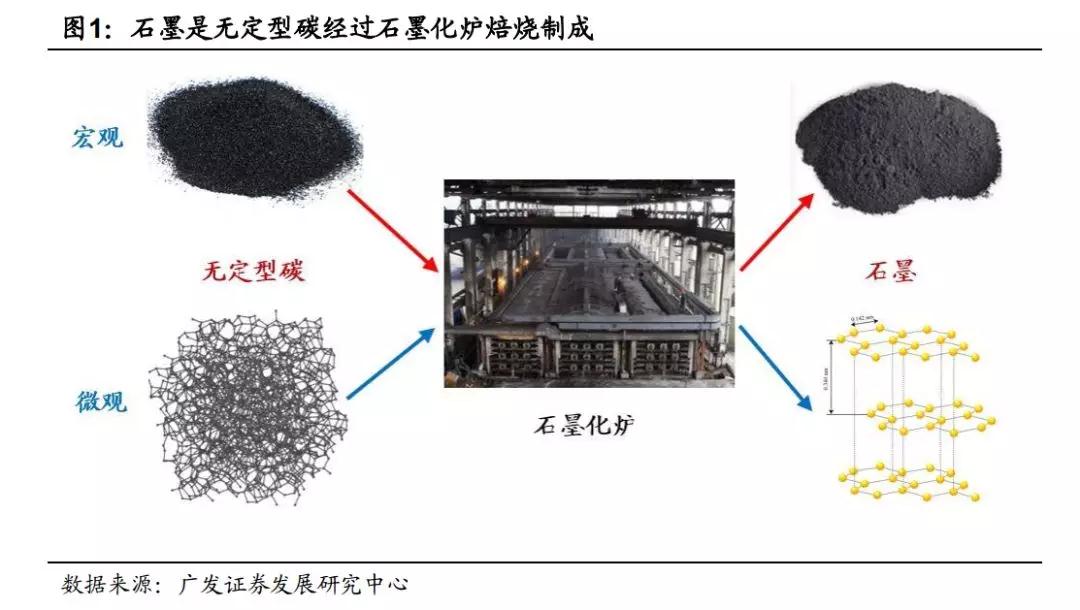
(二)生产工艺:石油焦、针状焦、煤沥青等原材料成本占比66.88%,生产周期超50天、超高功率长达65天
1、原料与成本:石油焦、针状焦和煤沥青等原材料占石墨电极成本的66.88%
(1)原料:低硫石油焦、煤系针状焦为骨材,煤沥青为粘结剂
石墨电极由石油焦、针状焦等为原料、煤沥青等为粘结剂,经原料破碎、配料、混捍、压制成型、焙烧、浸渍、二次焙烧、石墨化、机加工、质量检验、打包出厂等11道工序制备而成。
石油焦:石油焦(Petroleum coke)是原油经蒸馏将轻、重质油分离后,重质油再经热裂过程得到的石油制品。石油焦色黑多孔,碳含量占80%以上,灰分含量一般在0.5%以下,在化工、冶金等行业中有广泛的用途,是生产人造石墨制品及电解铝用炭素制品的主要原料。石油焦按硫分的高低区分,可分为高硫焦(含硫1.5%以上)、中硫焦(含硫0.5%~1.5%)、和低硫焦(含硫0.5%以下)三种,石墨电极及其它人造石墨制品生产一般使用低硫焦生产。

煤沥青:煤沥青是煤焦油深加工的主要产品之一,为多种碳氢化合物的混合物,成分较为复杂,常温下为黑色高粘度半固体或固体。按软化点高低分,煤沥青可分为低温、中温和高温煤沥青三种。煤沥青在石墨电极生产中作为粘结剂和浸渍剂使用,一般使用软化点适中、结焦值高的中温或中温改质煤沥青。
(2)成本:1吨成品石墨电极需1.02吨原料和0.29吨粘结剂,原材料成本占比达66.88%
石墨电极成本分四大部分,
一是石油焦、针状焦和煤沥青等原料成本,
二是焙烧、石墨化、机加工等生产工序的动力成本,
三是加工制造中的人力成本,
四是制造成本。
石墨电极的原料成本和动力成本为主要成本,占比达83.65%。根据中国炭素行业协会统计数据,2017年方大炭素的石墨电极产量居全国首位。方大炭素的炭素制品营业收入占公司总营收的75%,石墨电极产量占当年公司炭素制品总产量的85%,因此我们以典型石墨电极生产企业——方大炭素的2017年炭素制品成本构成作为石墨电极的成本构成是合理的。根据方大炭素2017年年报,炭素制品的成本构成中,原料成本、动力成本、人力成本和制造成本分别占66.88%、16.77%、8.02%和8.33%,其中原料成本相比2016年的51.83%大幅上升15个百分点。
1吨成品石墨电极需1.02吨原料和0.29吨粘结剂。根据2009年大连理工大学高勃硕士学位论文《国产针状焦生产超高功率石墨电极的研究》,石墨电极骨料为石油焦和针状焦,粘结剂为煤沥青,其基础配方为78%的骨料和22%的粘结剂。而根据张向军等人2001年发表在《炭素技术》期刊上的《用美国油系针状焦生产Φ400mmUHP石墨电极》一文,石墨电极在焙烧、石墨化等工序中会由于添加剂挥发或增加造成质量变化,在机加工等工序中会发生加工损失,其一次焙烧、浸渍、二次焙烧、石墨化和机加工成品率分别为90.4%、102.9%、96.97%、84.70%,因此其综合成品率为76.40%。即1吨成品石墨电极需最初原材料质量为1.31吨,对应骨料和粘结剂质量分别为1.02吨和0.29吨。
普通功率、高功率、超高功率石墨电极由于质量要求不同,制备时其骨料成分也不同。一般来说,普通功率石墨电极骨料均为石油焦,高功率石墨电极骨料由70%的优质石油焦和30%的针状焦组成,超高功率石墨电极骨料100%为针状焦。因此我们可计算出1吨普通功率石墨电极需石油焦骨料1.02吨;1吨高功率石墨电极骨料需石油焦0.71吨、针状焦0.31吨;1吨超高功率石墨电极骨料需针状焦1.02吨。
石墨电极生产成本受原材料价格影响较大。根据前文,石墨电极生产成本中原材料成本约占66.88%。尽管生产超高功率石墨电极所需针状焦成本要高于普通功率和高功率石墨电极,但超高功率石墨电极由于生产工序更多、加工精度要求更高,相应人力成本、制造成本和动力成本也会更高,因此我们假设普通功率、高功率和超高功率石墨电极原材料成本占比均为66.88%也是合理的。因此我们可以得到普通功率、高功率和超高功率石墨电极生产成本计算方法:
其中,CPC、CNC、CCT分别为石油焦、针状焦和煤沥青每吨单价。根据wind、卓创资讯数据,截止2018年3月16日,抚顺石化二厂1#A石油焦、锦州石化油系针状焦、华东地区煤沥青单价分别为8500元/吨、25000元/吨、3850元/吨,则计算可得普通功率、高功率和超高功率石墨电极成本分别为14633元/吨、22281元/吨、39797元/吨;根据中华商务网数据,截至2018年3月16日,国内直径500mm的普通功率、高功率和超高功率石墨电极主流市场价分别为67500元/吨、93333元/吨,155000元/吨,毛利率分别为78.32%、76.13%和74.32%。
2、生产工序与周期:生产工序达11道,普通功率石墨电极生产周期超50天,超高功率长达65天
石墨电极生产工序繁多。石墨电极由石油焦、针状焦等为原料、煤沥青等为粘结剂,经原料破碎、配料、混捍、压制成型、焙烧、浸渍、二次焙烧、石墨化、机加工、质量检验、打包出厂等11道工序制备而成,生产工序繁多。
普通石墨电极生产周期长达50天,超高功率至少需65天。典型普通功率石墨电极压制成型、焙烧、浸渍、焙烧、石墨化、机加工、成品打包等工序分别至少需要3天、25天、4天、15天、2天和1天的时间,共计50天,若考虑原料备货、原料破碎、配料、混捍、质检等工序,石墨电极的生产周期将会更长;而根据李圣华等2001年发表在《炭素科技》期刊上的《石墨电极生产中的节能降耗》一文,为了提高超高功率石墨电极的体积密度,采用先进的短流程生产工艺生产超高功率石墨电极需要一次浸渍和二次焙烧,二次焙烧需15天,因此超高功率石墨电极生产周期长达65天以上。石墨接头则需要二次浸渍和三次焙烧,生产周期更长。
(三)发展趋势:电弧炉功率提高驱动石墨电极向超高功率方向发展
1、100~150吨级高功率和超高功率电弧炉是主流发展方向
根据宋华德等人1994年发表在《特殊钢》期刊上的《超高功率电弧炉技术概况》一文,电炉的生产能力决定于炉容量与单位输入功率。在单位功率水平相同时,生产能力随容量增大而提高。
电炉容量过小,不仅生产效率低,技术经济指标差,而且配备炉外精炼设备也比较困难;而容量在150吨以上的电炉由于其单位功率水平不高,反而不能充分发挥超高功率电炉的优点,因此多数电炉容量在150吨内;同时,根据我国发改委于2017年发布的《产业结构调整指导目录2011年本(修正)》,30吨以下容量的电炉已经被列为落后产能予以淘汰,而30~100吨容量的电炉被列为限制类建设项目。因此100~150吨高功率和超高功率电弧炉将是我国未来电弧炉发展方向。
2、电弧炉功率提高驱动直径500mm以上的高功率和超高功率石墨电极发展
超高功率电弧炉发展驱动超高功率石墨电极需求。随着劳动效率高、综合成本低的大容量超高功率电弧炉的日趋增多,对电弧炉用石墨电极的最大允许电流也提出了更高的要求。根据天津大学张勇2004年硕士学位论文《φ700mm超高功率石墨电极接头的研制》,电弧炉用石墨电极最大允许电流与石墨电极的直径成正相关。因此为满足超高功率电弧炉的使用工况,发展大直径的石墨电极势在必行。
直径为500mm以上的超高功率石墨电极的生产和使用将占据主导地位。根据天津大学张勇2004年硕士学位论文《φ700mm超高功率石墨电极接头的研制》,100吨以上的电弧炉所用的石墨电极的直径均在500mm以上,因此未来直径在500mm以上的超高功率石墨电极的生产和使用将占据主导地位。
石墨电极高功率化趋势对石墨电极的性能提出了更高的要求。普通功率石墨电极允许使用电流密度低于17A/cm2,主要用于炼钢、炼硅、炼黄磷等普通功率电弧炉;高功率石墨电极允许使用的电流密度为18~25A/cm2,主要用于炼钢的高功率电弧炉;超高功率石墨电极允许使用的电流密度大于25A/cm2,主要用于炼钢的超高功率电弧炉。普通功率、高功率及超高功率石墨电极在直径、电阻率、抗弯强度、抗拉强度、弹性模量、灰分等物理、化学性能参数上也有差异。超高功率石墨电极的各项物化性能较普通功率、高功率石墨电极更为优异,产品定位也更加高端。
二、石墨电极:电弧炉炼钢关键耗材、原料成本占比达66.88%,超高功率化是发展方向
(一)应用领域:电弧炉炼钢关键耗材,吨钢消耗量在1.2~2.5 千克/吨,平均为2.0千克/吨
1、炼钢电弧炉中加热导体通常采用石墨材料,中频感应炉并不使用石墨电极
炼钢电弧炉中的加热导体通常采用石墨材料制造。电弧炉工艺灵活性好,能有效地除去硫、磷等杂质,炉温容易控制,且设备占地面积小,适于优质合金钢的熔炼。由于石墨材料是唯一具有良好导电性和导热性的非金属材料,其导电性是不锈钢的4倍,且导电系数随温度升高而降低,同时具有很低的热膨胀系数,因此电弧炉中以电弧形式释放电能对炉料进行加热熔化的导体通常采用石墨材料。
石墨电极在电弧炉中使用时由具有内螺纹孔的石墨电极本体和具有外螺纹的石墨电极接头组合连接使用。电极在炼钢炉上使用时依靠加工成公螺纹和相应尺寸的母螺纹将上下3~4根电极连接起来实现连续使用。
2、消耗强度:吨钢消耗量在1.2~2.5 千克/吨,100吨交流电弧炉初装消耗量5.34~7.12吨、年均消耗量可达1480吨
石墨电极是易耗品,不同类型电弧炉石墨电极消耗量在1.2~2.5 kg/t之间,受多因素影响而不同。根据B.Bowman等人在《炭素技术》期刊上发表的《电弧炉中石墨电极的消耗》一文,石墨电极消耗方式可分为端部消耗、侧面氧化消耗、残端损失以及根部折断四种方式;石墨电极其消耗量及消耗速度受电炉电流大小、生产能力、实际氧量、实际连接、废钢种类和装料方式等多方面的影响。根据高占彪等人2009年在《炭素技术》期刊上发表的《对电弧炉冶炼中石墨电极消耗及使用的探讨》一文,电弧炉吨钢石墨电极消耗在1.2kg/t至2.5kg/t之间;不同类型的电弧炉其石墨电极消耗量也不同,直流电炉石墨电极消耗量相比交流电炉和电阻电炉偏低。
100吨交流电弧炉初始安装需石墨电极5.34~7.12吨。根据李京社等人2013年在全国炭素技术暨节能减排交流大会上发表的《电弧炉石墨电极成本控制》一文,交流电弧炉有三根石墨电极,每根石墨电极由3~4支电极以锥形电极接头链接在一起组成。因此,每台交流电弧炉在初始安装时有9~12支石墨电极。假设100吨交流电弧采用直径为500 mm的石墨电极,常见石墨电极本体长度为1800mm;根据前文所述,超高功率石墨电极的体积密度在1.64~1.71 g/cm3,取平均值1.68g/cm3,则单支石墨电极本体的质量为593.5kg=3.14×(500÷2)2×1800×1.68÷106。因此单台交流电弧炉初始安装时石墨电极用量为5.34~7.12吨。
100吨交流电弧炉平均年石墨电极消耗量达1480吨。根据前文的测算,100吨交流电弧炉年产量在66~81万吨,取平均值74万吨。同样根据前文所述,交流电弧炉石墨电极消耗量在1.5~2.5 kg/t之间,取平均值2kg/t。则可计算得到100吨交流电弧炉年石墨电极消耗量达1480吨=74×104×2÷103。
(二)存量需求:2017年国内石墨电极表观消费量仅增长3.06%,海外石墨电极表观消费量大增10.56%,是国内产量增长核心驱动力
1、国内:2017年国内石墨电极表观消费量35.36万吨,同比仅小幅增长3.06%,占全球石墨电极需求总量的32.23%
2017年我国石墨电极产量达59.09万吨,出口量大幅增长47.39%至23.72万吨,表观消费量35.36万吨,国内石墨电极需求拉动有限,海外电弧炉对石墨电极需求增长是国内石墨电极产量增长的核心驱动力。根据中国炭素行业协会统计数据,2017年我国石墨电极产量达59.09万吨,同比2016年大幅增长17.22%;2017年我国石墨电极出口量达23.73万吨,同比2016年大幅增长47.39%,由此可得2017年我国石墨电极表观消费量为35.36万吨,同比2016年仅小幅增长3.06%,国内石墨电极需求对石墨电极产量拉动作用有限;因此海外电弧炉对石墨电极需求增长是国内石墨电极产量增长的核心驱动力。
国内超高功率石墨电极表观消费量自2011年以来连续5年出现下降,2016年仅为10.28万吨,占同期石墨电极表观消费量的29.96%。根据方大炭素2017年年报,2017年我国超高功率石墨电极产量达19.24万吨,同比2016年大幅增长42.62%,增速显著快于石墨电极产量增速;国内超高功率石墨电极表观消费量自2011年以来连续5年出现下降,2016年国内超高功率石墨电极表观消费量为10.28万吨,同比2015年大幅下降22.12%,仅占同期石墨电极表观消费量的29.96%。
2、海外:2017年海外石墨电极表观消费量为79.77万吨,同比2016年大增10.56%,占全球石墨电极需求总量的67.77%
若要得到海外石墨电极表观消费量,则需首先确定海外石墨电极产量。根据我们于2018年3月17日发布的《炼钢工艺发展路径专题之二:短流程发展箭在弦上?--政策、环保带来机遇,人才、技术仍有挑战,提高废钢回收率是关键前提》深度报告,我们采取两种方法对海外石墨电极进行测算并相互验证,得到2016年海外石墨电极产量预计为56.05万吨。
方法1:根据国际钢铁协会统计数据,2016年全球电炉钢产量为41842.4万吨,扣除中国5170万吨,则2016年海外电炉钢产量为36672.4万吨。若按前文所述,炼钢用石墨电极平均消耗量为1.95kg/t计算,2016年海外电弧炉石墨电极需求量为71.51万吨。根据中国炭素行业协会统计数据,2016年我国石墨电极出口16.1万吨,则可估算2016年海外石墨电极产量为55.41=71.51-16.1万吨。
方法2:根据美国石墨电极龙头企业Graftech公司2016年年报,公司预计2016年全球石墨电极总产能为170万吨,产能利用率为63%,则可计算得到2016年全球石墨电极产量为107.1万吨,由于2016年国内石墨电极销量为50.41万吨,则海外石墨电极产量为56.69=107.1-50.41(万吨),这与我们按照石墨电极平均消耗量测算结果基本一致;取两种测算方法均值,2016年海外石墨电极产量为56.05万吨,占全球石墨电极产量的52.65%;2016年中国石墨电极产量为50.41万吨,占比为47.35%。
2016年海外自中国净进口石墨电极16.10万吨,则2016年海外石墨电极表观消费量为72.15= 56.05 + 16.10(万吨);限于数据可得性,假设2017年海外石墨电极产量维持2016年水平,则2017年海外石墨电极表观消费量为79.77= 56.05 + 23.72(万吨),同比2016年增长10.56%,占全球石墨电极需求总量的67.77%。
(三)增量需求:预计18~20年全球将新增石墨电极需求28.38万吨,需求年均复合增速达4.88%
根据我们于2018年3月6日发布的《炼钢工艺发展路径专题之一:短流程VS长流程-环保与经济性加速短流程发展,上游原材料及耗材产业链或受益》深度报告,经合组织(OECD)于2017年8月7日发布的《CAPACITYDEVELOPMENTS IN THE WORLD STEEL INDUSTRY》(全球钢铁工业产能发展)报告统计了2017年海外在建短流程电弧炉产能为3676.2万吨,2018~2019年计划新建电弧炉产能为8835.5万吨;国内已官方宣布进行产能置换需淘汰的炼钢产能共计4059万吨,其中电炉炼钢产能2010万吨,高炉-转炉炼钢产能2049万吨;产能置换新建电弧炉设计产能为3118万吨。
为了计算海外及国内未来新增电弧炉产能对石墨电极特别是超高功率石墨电极的需求,我们做如下假设:
假设1:考虑到电弧炉投产周期在4~6个月,则假设2017年海外在建电弧炉中1/2产能在2018年投产,1/2产能在2019年投产;2018年计划新建电弧炉中,1/2产能在18年投产,1/2产能在19年投产;2019年计划新建电弧炉中,1/2产能在19年投产,1/2产能在20年投产,则可计算得到,2018、2019年海外新增电弧炉产能分别为4046.98、6253.85万吨,2020年至少为2208.88万吨。
假设2:由于2017年国内淘汰的2010万吨电炉炼钢产能则可能处于停产或者处于部分生产的状态,因此我们可以假设三种情况,即:
(1)2010万吨淘汰电弧炉原处于停产状态,则国内最大新增石墨电极需求对应的电弧炉产能为3118万吨;
(2)2010万吨淘汰电弧炉均处于在产状态,则国内最小新增石墨电极需求对应的电弧炉产能为1108=3118-2010万吨;
(3)2010万吨淘汰电弧炉50%处于在产状态,则国内将新增石墨电极需求对应的电弧炉产能为2113=3118-2010/2万吨;
假设3:假设2018、2019年国内将新建电弧炉产能均与2017年淘汰电弧炉50%在产时的电弧炉产能一致,为2113万吨。其中2017年新建电弧炉1/2将在2018年投产,1/2在2019年投产;2018年新建的电弧炉产能中1/2在2018年投产,1/2在2019年投产;2019年新建的电弧炉产能中1/2在2019年投产,1/2在2020年投产。则可计算得到,2018、2019年国内新增电弧炉产能分别为2113.0、3169.5万吨,2020年至少为1056.5万吨;
假设4:电弧炉产能利用率为2017年全国粗钢平均产能利用率77.22%。详细测算过程参见我们于2017年12月15日发布的《钢铁行业2018年年度投资策略:去产能、去杠杆、环保高压、兼并重组共筑钢铁新常态》深度报告;
假设5:假设海外在建电弧炉及国内通过产能置换新增电弧炉均采用的是超高功率石墨电极(UHP),吨钢UHP石墨电极消耗量为1.95kg/t。根据中国炭素行业协会和海关总署数据,2016年我国电炉钢产量为5170万吨,超高功率石墨电极产量为13.49万吨,销量为13.30万吨,出口量为3.21万吨,则我国国内炼钢用超高功率石墨电极总消耗量为10.09万吨,可计算得到2016年我国吨钢石墨电极消耗量为1.95=10.09×1000÷5170(kg/t),这与高占彪等人2009年在《炭素技术》期刊上发表的《对电弧炉冶炼中石墨电极消耗及使用的探讨》一文中三相交流电弧炉吨钢石墨电极消耗在1.5~2.5kg/t,平均为2.0 kg/t的结论基本吻合;
根据以上假设条件,我们预计2018、2019、2020年全球或将分别新增UHP石墨电极需求9.27、14.19和4.92万吨,2018~2020年合计或将新增UHP石墨电极需求28.38万吨,即到2020年全球石墨电极总需求量将达134.84万吨,18~20年全球石墨电极需求复合增速达4.88%。
三、供给端:2017年海外、国内产能利用率分别仅72%、64%,国内在建项目产能52.4万吨,年均复合增速或达13.18%
(一)存量供给:170万吨产能,海外产能去化显著,国内环保停限产压制产量释放,17年产能利用率分别仅为72%、64%
1、海外:产能由12年95.8万吨大幅下滑至17年72.6万吨,产能利用率仅71.86%,18年仅日本昭和新增3万吨产能
2017年海外石墨电极产能为78万吨,产能利用率为71.86%。根据日本Showa Denko于2017年12月12日发布的《Medium-term BusinessPlan "Project 2020+" Progress in 2017;Tasks and Strategies for 2018》报告,Showa Denko公司预计2017年全球(除中国外)石墨电极产能为78万吨;根据前文所述,2016年海外石墨电极产量估算为56.05万吨,假设2017年海外石墨电极产量维持2016年水平,则2017年海外石墨电极厂商产能利用率为71.86%。
2017年7家海外龙头石墨电极厂商产能市占率为93.08%,日本Showa Denko为海外产能最大石墨电极厂商。根据印度石墨电极巨头Graphite IndiaLimited于2017年10月发布的《Graphite India Limited Corporate Presentation(2017/10)》,2017年海外主要石墨电极生产企业产能情况为:日本Showa Denko、美国Graftech、印度Graphite India、HEG、日本Tokai Carbon、SEC和Nippon Carbon2017年产能分别约为25万吨、16.2万吨、9.8万吨、8.0万吨、7.8万吨、3.0万吨和2.8万吨,合计72.6万吨;根据Showa Denko于2017年12月12日发布的《Medium-term BusinessPlan "Project 2020+" Progress in 2017;Tasks and Strategies for 2018》报告,Showa Denko公司预计2017年全球(除中国外)石墨电极产能为78万吨,即7家海外龙头石墨电极厂商2017年产能市占率为93.08%。
合并、去产能,7大海外石墨电极厂商产能由2012年的95.8万吨大幅下降24.22%至2017年的72.6万吨。根据印度石墨电极巨头Graphite IndiaLimited于2017年10月发布的《Graphite India Limited Corporate Presentation(2017/10)》,受制于行业景气度降低、利润下降等影响,海外石墨巨头自2012年以来进行了多次减产、合并。德国SGL公司于2016年10月份将石墨电极业务出售给了日本的Showa Denko,后者也成为海外最大的石墨电极厂商,2017年其产能为25万吨,仅为2012年的69.44%;产能排名第二位的美国Graftech公司2017年产能为16.2万吨,仅为2012年的61.83%;印度Graphite India、HEG、日本SEC和Nippon Carbon则基本没有去产能。综合来看,7家海外石墨电极厂商产能由2012年的95.8万吨大幅下降24.22%至2017年的72.6万吨。
2、国内:民企为主、多分布于京津冀及周边地区,92万吨产能,产能利用率仅64.23%,环保限产压制产能释放
2017年我国石墨电极产能为92万吨,产能利用率仅64.23%;超高功率石墨电极产量占比仅32.56%,仍供不应求。根据前文所述,Graftech公司预计2016年全球石墨电极总产能为170万吨,Showa Denko公司预计2017年全球(除中国外)石墨电极产能为78万吨,若2017年全球总产能保持2016年规模,则2017年我国石墨电极产能为92万吨。按2017年我国石墨电极产量59.09万吨计算,我国石墨电极行业产能利用率仅为64.23%;但值得注意的是,随着中国冶金产业结构的优化升级,落后生产装备的小电炉日渐被淘汰,高功率和超高功率电炉迅速发展,从而使普通功率中小规格石墨电极市场供需大大萎缩,产品严重过剩。超高功率、大规格石墨电极需求量逐年递增,但产能仍然不足,2016、2017年我国超高功率石墨电极产量仅占石墨电极总产量的26.76%、32.56%,提升空间仍很大。
2017年我国石墨电极产量为59.09万吨,同比增长15.71%,结束自2011年来下滑态势。根据方大炭素股份有限公司2017年年度报告,据中国炭素行业协会不完全统计,2017年1-12月石墨电极产量为59.09万吨,与上年同期相比增长15.71%。石墨电极销售量59.17万吨,与上年同期相比增长率为19.88%。其中,超高功率石墨电极的产销量相对于上年同期分别增长42.64%、42.24%。
方大炭素石墨电极市占率全国第一,2016年产量占比超28%。根据中国炭素行业协会发布的2016年我国炭素行业运行情况和方大炭素201年年报,2016年方大炭素石墨电极产量达14.2万吨,占2016年全国石墨电极总产量的28.17%,市场占有率居全国首位。从超高功率石墨电极看,CR4达71.55%,方大炭素产量居首:根据中国炭素行业协会发布的2016年我国炭素行业运行情况,2016年我国超高功率石墨电极产量13.49万吨,同比2015年下降17.47%,其中方大炭素、南通扬子炭素、吉林炭素、开封炭素四家企业产量排名居前,其超高功率石墨电极产量占全国总产量比例高达71.55%。
京津冀及周边地区对石墨炭素企业关停限产,压制石墨炭素企业产能、产量释放。根据中国炭素行业协会统计数据,河南、山东和湖南列全国石墨及炭素制品产量排名前三位,占比分别为29%、19%和7.95%;河南、山东、山西、河北、天津和北京等京津冀及周边地区石墨和炭素制品产量就占全国总产量的54%左右;2017年2月,发改委、环保部联合北京市、天津市、河北省、河南省、山东省和山西省人民政府,发布了《京津冀及周边地区2017年大气污染防治工作方案》,规定“炭素企业达不到特别排放限值的,全部停产,达到特别排放限值的,限产50%以上,以生产线计”。石家庄市、济宁市、天津市等地市也相继发布了炭素行业环保限产、停产要求。
(二)增量供给:18年海外仅3万吨新增产能,国内在建项目产能达52.4万吨,国内石墨电极总供给年均复合增速达13.18%
1、海外:18年仅日本Showa Denko计划新增3万吨产能
Showa Denko预计2018年新投产3万吨石墨电极产能,其他公司或以提升产能利用率为主要增产手段。根据Showa Denko于2017年12月12日发布的《Medium-term Business Plan "Project2020+" Progress in 2017;Tasks and Strategiesfor 2018》报告,公司2017年位于日本、美国和欧洲的工厂均已达到满产,现有工厂产能利用率提升空间较小,公司位于美国的新工厂将于2018年投产,预计新增产能3万吨,即2018年公司产能将达28万吨。根据其他公司年报和已有公告,尚未获得其他公司扩大石墨电极产能的计划,即短期内其他龙头企业或主要以提升已有产线的产能利用率来增产。
2、国内:现有企业或可通过优化生产工序增产,新增产能或至少达52.4万吨,18~20年我国石墨电极产能年均复合增速或达13.18%
高价格、高盈利刺激下石墨电极企业或通过革新生产技术、优化生产工序的方式提升产能利用率实现增产。根据中泽集团官网2017年7月27日新闻《吉林炭素推进转型升级提高生产经营水平》一文,吉林炭素有限公司通过优化生产工序,在焙烧工序将隧道窑装车数量由12车增加至14车,预计2017年8月~12月增加产量200吨/月;在石墨化工序采取扩大炉芯装炉,预计2017年8月~12月增加产量200吨/月;从理性经济人角度考虑,在目前石墨电极高价格、高盈利刺激下石墨电极企业倾向于通过革新生产技术、优化生产工序的方式提升产能利用率实现增产。
2017年来国内投产、在建、拟建的石墨电极项目总产能至少为52.4万吨,其中6万吨超高功率石墨电极产能已投产。我们统计了2017年以来全国各地市投产、在建、拟建的石墨电极项目及项目进度情况,如表10所示。2017年下半年以来国内投产、在建、拟建的石墨电极项目总产能至少为52.4万吨,相当于2017年我国石墨电极产能的56.96%。其中,截止2018年3月22日,介休市龙凤炭素2万吨超高功率石墨电极项目、大同腾扬科技有限公司2万吨超高功率石墨电极项目、乌兰察布市旭峰炭素10万吨超高功率石墨电极项目一期(2万吨)已建成投产,合计产能达6万吨,且均为超高功率石墨电极。
我们估算18~20年我国分别将会有5.25、25.45和41.4万吨石墨电极产能投放,年均复合增速将达13.18%。假设2017年底投产项目2018年处于产量爬坡阶段,仅能释放50%设计产能,2019年完全达产;同样,2018年底投产项目2019年处于产量爬坡阶段,仅能释放1/2设计产能,2020年完全达产;对于2018年6月投产项目,我们假设2018年当年能够释放25%设计产能,2019年释放75%产能,2020年完全达产。
根据以上假设,我们估测了2017年来国内投产、在建、拟建的石墨电极项目在2018~2020年的产能投放进度,如表11所示,预计18~20年我国分别将会有5.25、25.45和41.4万吨石墨电极产能投放,2020年我国石墨电极产能将达133.4万吨,年均复合增速将达13.18%。
四、供需平衡:预计2018年全球石墨电极供需基本平衡,2019、2020年石墨电极或供大于求
需求端:预计2020年全球石墨电极总需求将达143.52万吨,18~20年年均复合增速达4.88%。根据前文所述,2020年前预计海外及国内新建电弧炉或将新增石墨电极需求合计28.38万吨,其中2018、2019、2020年将分别新增UHP石墨电极需求9.27、14.19和4.92万吨,即2018~2020年全球石墨电极需求量将分别为124.41、138.60、143.52万吨,年均复合增速达8.29%。
供给端:预计2020年全球石墨电极总供给将达159.54万吨,18~20年年均复合增速达8.94%。根据前文所述,2018年海外仅日本昭和新增3万吨产能,假设2019、2020年海外均不新增产能,即新增产能全部来自国内;假设新增产能均能够满产,则预计2020年全球石墨电极总供给达159.54万吨,18~20年年均复合增速达13.18%。
预计2018年全球石墨电极供需基本平衡,2019、2020年石墨电极或供大于求。对比表12和表13,我们可得,若新增产能均能够满产,则2018年供需缺口为1万吨,考虑到原有产能或可通过提高产能利用率实现增产填平供需缺口,因此2018年全球石墨电极或处于供需基本平衡的状态;而2019年以后,随着国内新建石墨电极项目的达产,全球石墨电极总供给开始大于总需求,即2019、2020年全球石墨电极市场或处于供大于求的状态。
五、建议:长流程置换短流程成理性选择,2020年前石墨电极或不会成为短流程发展掣肘
政策鼓励短流程,环保限产常态化、超净排放推高环保成本,长流程置换短流程成理性选择。我们于2018年3月17日发布了《炼钢工艺发展路径专题之二:短流程发展箭在弦上?--政策、环保带来机遇,人才、技术仍有挑战,提高废钢回收率是关键前提》深度报告,认为:
在政策方面,国家正在系统研究支持电炉钢发展的配套政策措施,允许退出转炉建设电炉的项目可实施等量置换,鼓励现有高炉-转炉长流程企业转型为电炉企业,产业政策导向十分明显;
在环保方面,短流程在污染物排放、吨钢能耗以及环保成本方面拥有优势。在钢铁行业特别是长流程炼钢环保限产常态化、长流程超低排放改造启动的大背景下,长流程炼钢产能置换为短流程已经成为可行的选择之一;
2019、2020年石墨电极市场或供大于求,石墨电极不会成为短流程发展掣肘。
需求端看,根据前文所述,2017年海外在建短流程电弧炉产能为3676.2万吨,2018~2019年计划新建电弧炉产能为8835.5万吨,国内已官方宣布进行产能置换新建电弧炉设计产能为3118万吨,全球短流程快速发展将直接增加石墨电极需求;
供给端看,已统计到的国内在建石墨电极项目总产能达52.4万吨,即使海外19~20年不再新增产能且产能利用率均不再提升,2019年、2020年全球石墨电极仍然会供过于求,因此石墨电极不会成为短流程发展掣肘。
来源:广发钢铁新材料 分析师:李莎
(以上文章系转载,并不代表广州鸿凯机械科技有限公司观点,如涉及版权等问题,请联系我们以便处理)
