高级会员
已认证
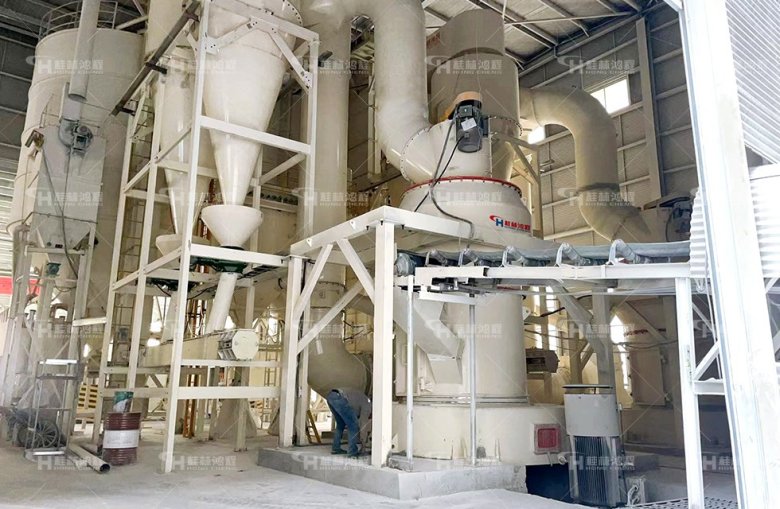
随着我国对火电厂二氧化硫排放标准的日益严格,90%以上的燃煤电厂采用石灰石-石膏湿法脱硫工艺,石灰石粉作为核心脱硫剂,其细度与粒径分布直接决定了脱硫效率。实验数据表明,当石灰石粉细度达到325目(44μm)筛余≤5% 时,比表面积增大,可显著提升与二氧化硫的反应速率和钙利用率15。而实现这一细度目标的关键,在于选择高效、可靠的粉磨设备。目前主流工艺聚焦于立式磨粉机(立磨)与升级型雷蒙磨两大技术路线,二者在能耗、产量和适用场景上差异显著。
一、立式磨粉机:大型电厂的节能优选
立磨凭借其一体化设计(破碎+研磨+分级)成为大型脱硫项目的理想选择。其核心优势在于能耗比球磨机低30%-40%,且单机产能轻松突破20t/h,大型号(如HLM3400)更可达100-120t/h。
关键技术亮点包括:
粒度精准控制:采用涡流分级技术,确保成品中>44μm的颗粒趋近于零,满足超低排放对石灰石活性的严苛要求;
能源循环利用:可直接接入电厂蒸汽热源烘干含水分≤5%的原料,减少燃煤污染,降低运营成本;
环保闭环设计:负压系统配合99.99%收尘效率的脉冲布袋除尘,实现粉尘近零外溢。
对于年处理量超10万吨的电厂,立磨的吨粉电耗优势可在半年内抵消初始投资差价。
二、雷蒙磨升级方案:中小规模项目的灵活之选
针对中小型脱硫需求(≤25t/h),新一代纵摆结构雷蒙磨展现出强劲竞争力。以HC1700型为代表,其通过三项技术实现性能跃升:
阶梯式磨辊-磨环设计:延长物料碾压路径,离心碾压力提升35%,产量达传统5R雷蒙磨的2.5倍(6-25t/h);
强制涡轮分级系统:支持80-400目(0.18-0.038mm)无级调细,覆盖炉内干法脱硫(粗粉)与湿法脱硫(细粉)双重要求;
模块化维护结构:磨辊总成采用多层密封和快拆设计,维护周期延长40%,降低停机损失。
相较于立磨,雷蒙磨的占地面积减少50%,且初始投资更低,适合用地紧张或预算有限的项目。
三、实战案例:设备选型需匹配工艺目标
某300MW电厂在脱硫改造中面临两套方案抉择:
方案A:采用HLM2400立磨,产量70t/h,细度325目通过率95%,但需配套蒸汽烘干系统;
方案B:配置2台HC1700雷蒙磨,总产量50t/h,细度250-325目可调,可直接利用预干燥原料。
经综合评估,该厂因原料含水率仅3%且需兼顾炉内脱硫粗粉需求,最终选择方案B。运行数据显示,吨粉电耗较旧球磨系统下降33%,且分级出的粗粉(80-150目)回用于CFB炉内脱硫,实现资源全效利用。
经验启示:湿法脱硫需优先保障细度(325目占比≥90%),而循环流化床(CFB)电厂宜选用可分级产出粗/细双粉体的设备,避免过细颗粒逃逸炉膛。
四、科学选型四要素:告别“参数陷阱”
为避免设备与需求错配,建议综合以下维度决策:
考量维度 | 立磨方案 | 雷蒙磨方案 |
---|---|---|
处理量需求 | >20t/h的大型连续生产 | ≤25t/h的中小型项目 |
原料特性 | 含水≤5%需烘干 | 含水<6%的干燥物料 |
细度灵活性 | 固定细度高精度 | 80-400目宽幅可调 |
投资回收周期 | 高投资 | 中低投资 |
额外关注:
场地限制:立磨需配套热风系统和大型收尘器,厂房高度要求≥15米;
智能控制:新型设备均支持PLC自动化(如HC1700),可减少人工干预。
结语
在脱硫石灰石粉制备领域,没有“最佳设备”,只有“适合设备”。立磨以单机高产能和超低电耗着力大型项目,而模块化雷蒙磨则以灵活细度与低投入成本服务中小需求。随着国家超低排放标准覆盖至钢铁、水泥等行业,高效磨粉技术将成为企业绿色转型的关键支点。
立即行动:获取定制化选型方案与试磨服务,请点击咨询——让专业工程师为您测算吨粉成本优化空间!联系电话:13687861989 伍工。
