高级会员
已认证
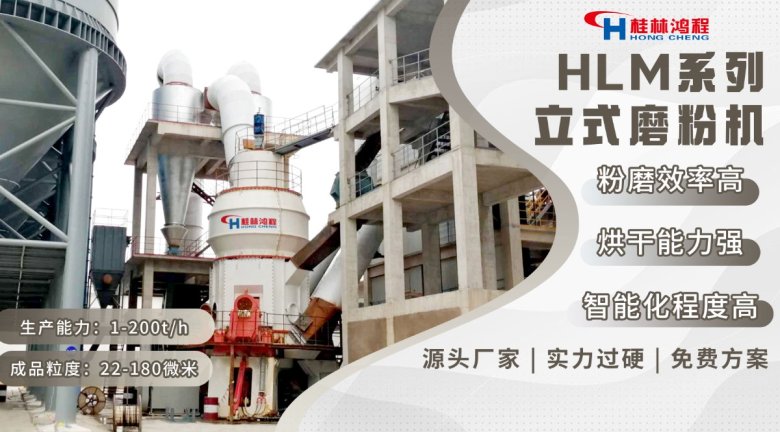
陶粒是一种轻质、多孔、具有一定强度的微细颗粒材料,常用于制造混凝土、陶土制品、填充材料等。在陶粒生产中,原料粉碎是一道重要的工序,将原料进行研磨,使之变成粉末状,通过陶粒砂磨粉机设备完成。桂林鸿程作为陶粒砂磨粉机生产厂家,今天为您介绍一下陶粒粉磨工艺对陶粒生产的重要性。
粉磨工艺是免烧陶粒的基础工艺,它奠定了陶粒的质量基础,特别是强度基础,并为造粒创造了条件。陶粒粉磨工艺对陶粒生产的重要性主要体现在以下几个方面:
一、提高废渣活性,赋予陶粒强度免烧陶粒主要以水泥和活性废渣为主要强度来源。它的相当部分强度均是由废渣的活性产生和赋予的,外加极少量的水泥(在蒸压条件下也可以不加),只是一种补充。因此,废渣活性的发挥程度也就决定了陶粒的强度。粉磨就是通过物理手段激发废渣的活性,提高它的胶凝性,增加陶粒的强度。活化剂属于化学活化,它必须和物理粉磨活化配合才能更好发挥作用。二者缺一不可。不经过粉磨工艺处理,废渣活性的发挥仅为30%~40%,经粉磨活化处理后,它的活性发挥可提高到80%100%。因此,粉磨对陶粒的强度起着关键性的作用。那么,粉磨为什么可以提高废渣的活性?
①打破了活性废渣特别是粉煤灰坚硬的玻璃体。粉磨使玻璃体产生裂纹、变粗糙或粉碎,使玻璃体内封闭的硅铝成分容易溶出,而活化成分容易进入。这样硅铝成分更容易和活化剂接触,产生反应激发作用,从而使硅铝成分更多地转化为硅酸盐和铝酸盐,产生类似水泥的胶凝作用而取代水泥。不经粉磨,由于废渣玻璃体的封闭作用,活化剂不易产生作用,硅铝成分也难以溶出。
②粉磨后,粒度变得更小,增加了活性废渣的比表面积,暴露和产生许多新表面,也就增加了活化剂和硅铝的接触面积,促进了活化反应。在粉磨之后,一个大颗粒可能会变成几百个、几千个甚至几万个小颗粒,表面积增加很多倍,活化剂在这些新表面上就可以更多地和活性废渣反应。另外,颗粒变得越小,从表面到颗粒中心的距离就越短,活化剂就更容易进入废渣颗粒的内部和中心与之反应,反应会进行的更彻底。
③在粉磨过程中,活化剂和废渣得到更均匀的混合,增加了它们的接触机会,扩大了它们的接触面积,也可以促进废渣的化学活化。
④在粉磨过程中,摩擦热很高,可使物料温度升高,使活性
废渣产生热激发作用,也可促使废渣活化。
二、物料磨细后,造粒质量大幅提高粉磨工艺不单单是粉磨废渣,而是全部物料的混合粉磨。在粉磨以后,废渣的细度得到大幅提高,变得更细。造粒实践已经证明,物料粉磨越细,造粒质量就越高,造粒质量越高,陶粒成本就越低,陶粒总体质量也就越好。不经粉磨的物料,粒度大,黏结性差,造粒后物料松散,密实度不够。这就使陶粒球坯的强度很差,在出盘以后的输送、堆放过程中大量破碎,成品率很低,导致产量下降,陶粒成本上升。粉磨以后,造粒密实,球坯表面光洁美观,不易破碎,提高了成品率。同时,由于陶粒球坯的初始强度好,也可增加后期强度,并降低陶粒的毛细孔率,也相应降低了吸水率陶粒的抗吸水性得到提。粉磨物料所生产的陶粒和没粉磨物料所生产的陶粒相比,质量相差一个档次。
综上所述,粉磨对免烧陶粒的生产,具有决定性的重要意义,绝不可小视。
三、粉磨工艺的技术要求粉磨的目的是让粒度变小,物料变细。原则上讲,物料以细为好,但如果粉磨过细,则会过增加电耗和粉磨人工费用,导致陶粒的成本上升,那也是不合算的。所以,粉磨的细度既要达到使用技术要求,又要不过大增大电耗和其他费用,应适可而止,并非越细越好。具体的粉磨技术要求如下。
①粉磨筛余量粉磨细度假如以筛余量来表征,宜控制在o.08方孔筛,筛余量小于3%;一般水泥的筛余量国标规定为小于10%,大多数水泥厂小于8%.少数厂小于5%。而陶粒混合料的粉磨细度更细一些,属于高细粉磨,宜小于3%为好。如果没有条件,磨机达不到这个要求,至少应控制在小于8%。
②粉磨比表面积比表面积越大,活化反应就进行的越好。因此,粉磨比表面积应尽量大一些。现在,水泥粉磨的比表面积约为300mz/kg,高细水泥的比表面积约为320~350mz/kg。陶粒混合料的比表面积应相当于高细水泥或者略细于水泥,控制在350~400m2/kg最好。最好能有1/4的活性废渣粉磨细度达到400-600mz/kg,可以采用超细粉磨。
③粉磨粒径分布粉磨活性废渣及水泥的粒径应有合理的级配。混合物料在粉磨以后,小于60tLm的颗粒应大于70%,10-301um颗粒应大于soH,小于lOUm颗粒应大于30%.小于5μm颗粒应大于10%。
桂林鸿程作为陶粒砂磨粉机生产厂家,我们生产的HLM系列立式磨粉机,是陶粒粉磨的理想设备,对于物料来源广泛的陶粒原料有良好的适应性,在陶粒生产中得到了成功的应用和良好的口碑。如果您有陶粒粉磨需求,欢迎给我们来电了解陶粒粉磨设备详情,联系电话:13687861989伍工
