金牌会员
已认证
1.前言
锂离子电池正负极材料是典型的粉体物质,其特性直接关联电池性能。电极粉体的形状、粒度、比表面积、内部结构、填充密度、表面特性等因素对电池的能量密度、输出特性、循环特性等有很大的影响。故电极材料的设计和加工成为一个重要的课题。总之电极材料决定电池性能所能达到的上限,而工艺过程则决定了其性能的下限,因此需要尽可能完善工艺过程,减少性能上下限之前的差异。
表面包覆是改性正负极材料的常用的有效方法之一,其可以有效的阻隔与电解液的直接接触,减小与电解液的副反应发生,同时也可以稳定结构,减轻相变应力,提升电芯的循环稳定性。然而电芯在实际生产中,需要经过非常复杂的工艺,比如用高速旋转搅拌机匀浆,用大压力辊压极片等等,这些工艺容易造包覆层脱落,颗粒破碎,涂层开裂,甚至材料结构变化等一系列问题,从而影响电芯的容量和寿命等性能。特别地,在Si基复合材料中,电极压延导致复合材料中的颗粒断裂、多孔设计结构的坍塌和用于稳定复合材料的最外碳包覆层的破裂。因此,电极压延导致电池性能的严重劣化。然而关于工艺过程对材料影响方面的报道较少见,本文主要使用不同压力对硅碳负极粉末进行平压后,并制作成浆料,监测其浆料产气量,从而量化压力对材料破坏程度。
2.测试信息
2.1 实验设备
测试设备1:原位产气体积监控仪,型号GVM2200;
测试设备2:粉末电阻率&压实密度仪,型号PRCD3100。
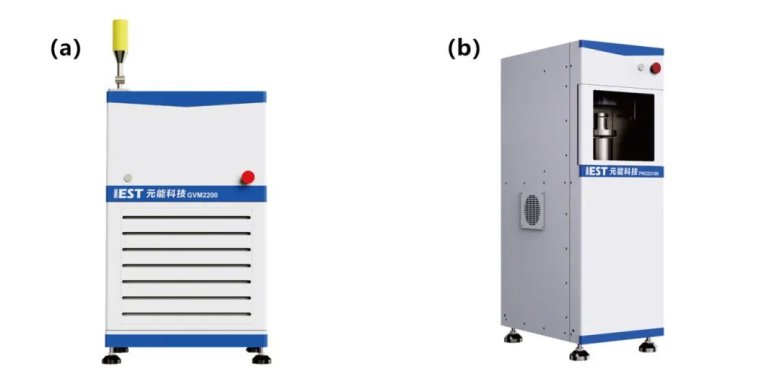
图1. (a)原位产气体积监控仪(GVM2200);(b)粉末电阻率&压实密度仪(PRCD3100)
3.实验过程及分析
锂电正负材料属于粉体材料,粉体材料在压缩过程中会经历如图2所示四个过程:受压初期颗粒间滑动或重新排列,以寻找更加紧密的堆积方式。这一过程主要依赖于颗粒间的摩擦力和相互作用力。随着压力继续增大颗粒发生弹性形变和塑性形变。如果压力进行一步增大,在极端情况下超过了其承受极限,颗粒可能会发生破碎或粉化现象。总之粉体颗粒在这些演变过程中都会对材料本身结构产生很大的影响。
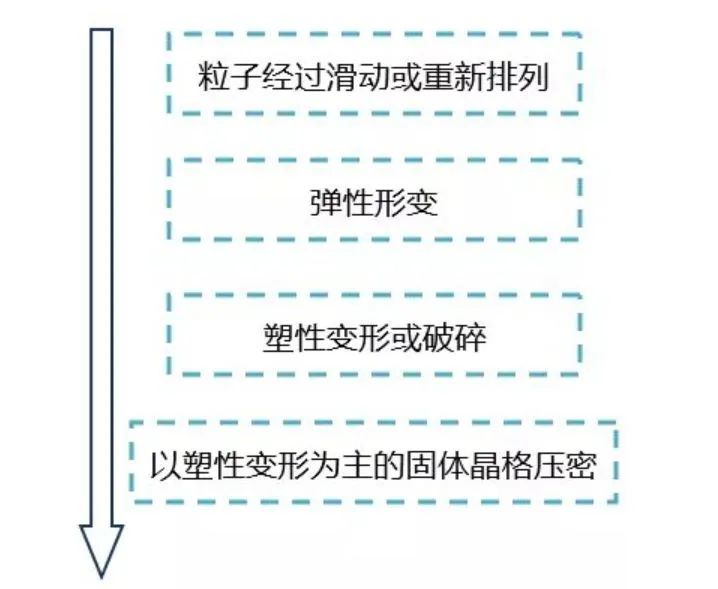
图2.粉体材料受压微观变化过程
3.1 电阻率及压实密度
选取硅碳负极材料,分成四组平行样,称量1.0g,然后再用元能科技的粉末电阻率&压实密度仪(PRCD3100),分别在10MPa,50MPa,100MPa,200MPa压力条件下,监测其在不同压力条件下的电导率及压实密度变化情况,如图3(a)所示:四个平行样品随着压力增大,电导率和压实密度都呈现增大趋势。图3(b)为样品从0~200MPa整个过程中压实密度和电导率的变化趋势,整个过程也呈现压实密度和电导率随压力增加不断增加的现象。
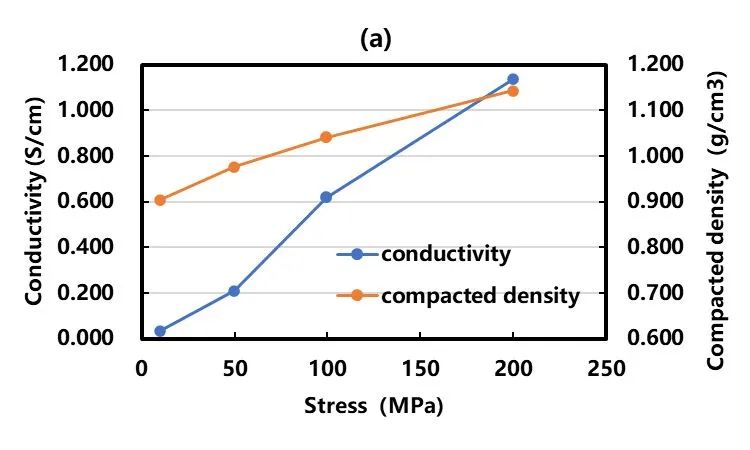
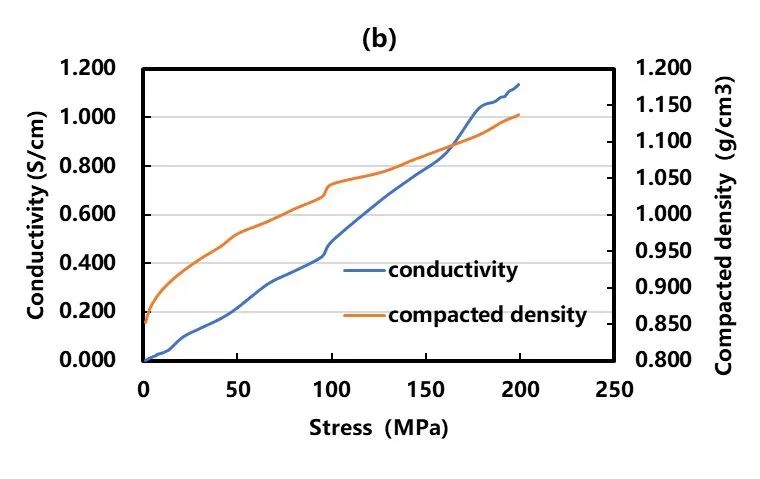
图3.硅碳粉末不同压力下电导率及压实密度变化曲线
从图2中我们知道粉体材料在受压时粒子间会受很强的相互作用,颗粒会发生重排,包覆层脱落,甚至会发生破碎等变化。这些现象与颗粒间机械接触应力,颗粒的弹塑性变形、摩擦力及表面能等有关系,具体需要考虑颗粒材料塑性能、杨氏模量、屈服强度、应变硬化等材料特性。结合图3变化趋势,结果说明此样品在受压过程中发生包覆层脱落和颗粒破碎的粒子可能仅有极小部分,其变化并未影响电子导电通路和整体厚度,即这种少量的包覆层脱落和颗粒破碎与电导率和压实密度关联性不大。
3.2 微观结构
用扫描电子显微镜(SEM)观测其微观结构,其中0MPa样品为未压样品,如图4所示:样品在50MPa前微观结构与不受压样品无明显差异,当压力达到100MPa后,在视野中可以找到颗粒破碎。一般,硅颗粒的杨氏模量为150GPa,屈服强度0.5~2GPa,而石墨材料杨氏模量50GPa,屈服强度约0.5GPa。在颗粒压缩过程中,通过施加压缩载荷并测量应变和应力的变化可以绘制应力应变曲线。压缩应力应变曲线通常具有以下几个特点:(1)弹性阶段,在开始施加载荷时,材料会发生弹性变形,即应变与应力成正比。这一阶段的斜率代表了材料的刚度。(2)屈服阶段,当载荷继续增加时,材料会发生塑性变形,即应变与应力不再成正比。在这个阶段,材料的应力会达到一个最大值,即为屈服强度。(3)塑性阶段,在屈服点之后,材料会发生持续的塑性变形。应力会随着应变的增加而逐渐减小。(4)断裂阶段当应力达到材料的极限强度时,材料会发生断裂。此时,应变会急剧增加,应力会迅速下降。颗粒出现裂纹,说明材料开始发生了断裂,压缩力超过了材料极限强度。这种情况下,电极颗粒不能保持原始的形貌和稳走性,电极性能会劣化。
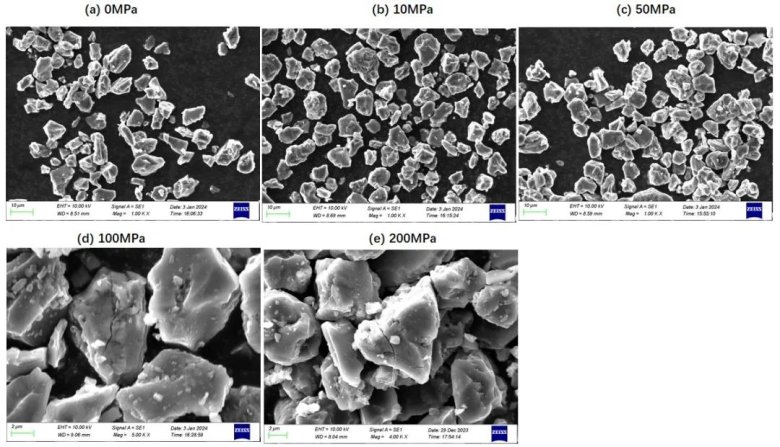
图4.不同压力条件下微观结构
3.3 浆料产气
虽然微观结构可以在一定程度上可分辨压力对硅基颗粒破碎的影响,但是区分度不明显并且难以进行量化。鉴于元素硅易水解,产生气态氢气 ,并且硅基材料常见的表面改性方法(表面包覆)是以硅为核心,并在外围包覆一层或多层碳材料,因而可以用硅基浆料产气量进行定量评估加工艺对材料结构影响。
按质量比为1:5(硅:去离子水)混合后密封于铝塑膜袋中,开启原位产气体积监控仪(GVM2200),并调节温度为40℃后,监测其产气体积变化,如图5所示:0MPa样品整个过程体积基本保持不变,说明样品本身包覆效果良好。随着样品受压压强增大,产气量呈现增加趋势,说明样品受压后确实存在包覆层脱落和颗粒破碎的现象,同时压力越大,这种破坏越严重。
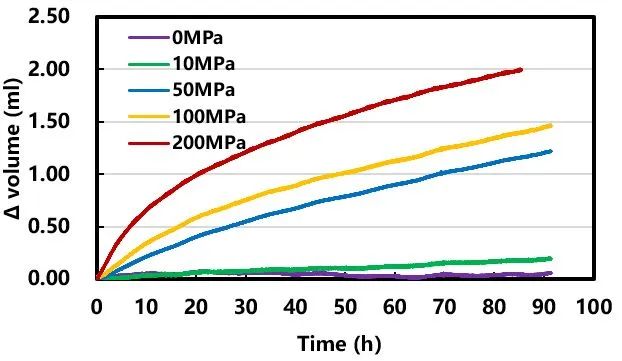
图5.不同压力对样品包覆效果影响
表面包覆改性硅基电极的辊压工艺需要特别注意施加压力的大小和压实程度。虽然大的压缩量能够增加颗粒之间的接触面积而提高电极的电子电导率,以及增加体积能量密度,但是必须避免过压情况。一方面,过压会增加孔隙迂曲度而降低离子传输特性,另一方面硅颗粒及其包覆层如果受到破坏,电极材料无法保证颗粒材料设计形成的抑制副反应和缓冲电极电化学膨胀的效果。因此,硅基电极辊压加工工艺需要仔细设计,综合平衡电池体积能量密度和电极机械稳定性。
4.小结
对于硅基负极材料,本文提出用浆料产气的方法表征制造工艺对硅基负极材料结构影响,并用原位产气体积监控仪(GVM2200)量化了不同压力对硅基负极粉体材料表面包覆和颗粒破坏程度,为硅基负极材料包覆强度提供一种新的表征方式,同时也可以通过量化指标优化电芯制作工艺,从而提升电芯性能。
