白金会员
已认证
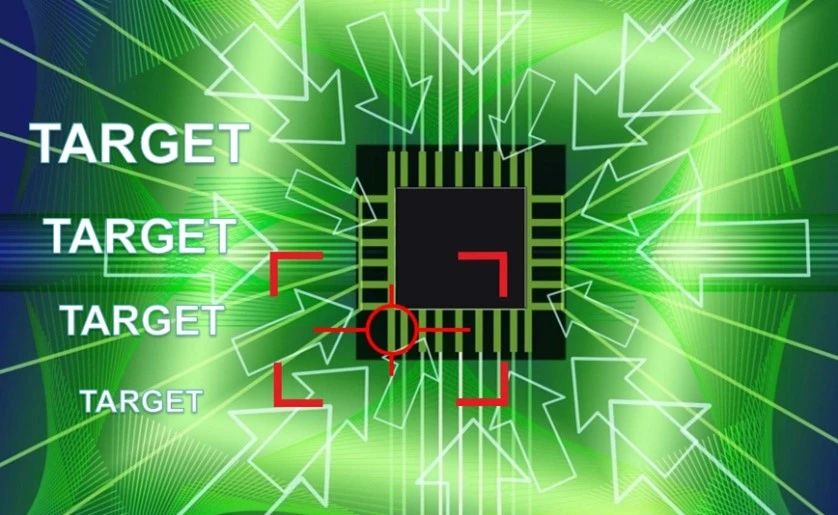
在材相制样领域,大多数时候对样品的制备位置并无特定的要求——制备可以在样品的任意高度位置进行,只要终抛效果满足要求即可。在这种情况下,操作人员无需担心制样的成功率,因为有足够的试错机会。但还有一大类制样是需要针对特定的点、面或区域而进行的,即目标金相制备,常见于微电子、失效分析、矿物、生物医药及机械制造等领域。目标制备具有位置敏感性,需要精确的材料定量磨削,因而对设备、耗材及操作人员的要求也相应提高。目标制备的典型应用场景包括以下内容,文中我们将逐一展开。
单个或少量样品的特定区域制备
制备目标为单个或少量样品的一个或几个特定区域,多用于实验室失效分析或结构连接处的微观检查。此种情况下由于样品的稀缺性及不可重新获得性,对制样位置精度及成功率的要求最高,很多技术人员习惯于手动制备以便随时观察位置。
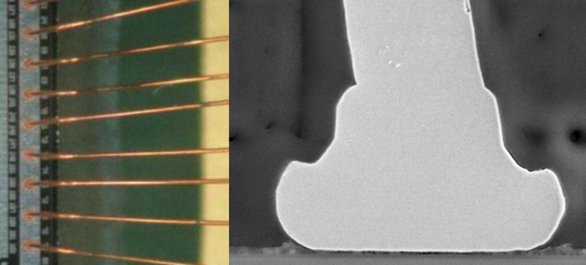
芯片引线键合处的目标制备
目标位置相同的大批量制备
原材料或元器件、工件的生产批次检测中,目标检测位置往往相同,比如PCB 厂商对特定电镀通孔、盲孔、埋孔等进行的切片抽检,或机械制造商对焊点、轴承等的工艺质量控制检测。此时制备效率通常是最主要的考量,当然前提是精度也需要达到规定要求。
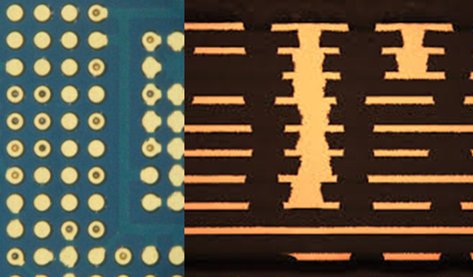
PCB原材料的埋孔目标制备
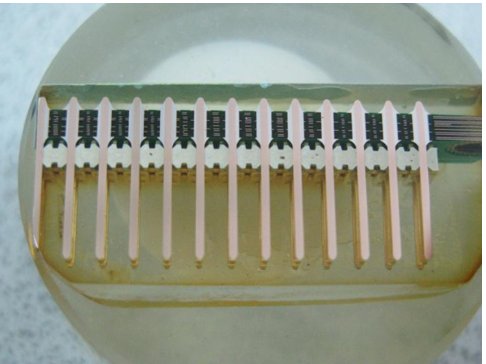
波峰焊焊点的目标制备
特定厚度的薄片样品制备
在岩相及生物及医学行业,除了常规的块体材料金相制备(光片制备)外,有时要将样品粘接到载玻片上,切割并定量磨削成几十微米的薄片,以便后续用透射光或偏振光进一步观察。薄片制备对象包括矿物类样品、鱼耳石等生物类样品以及细胞组织与血管支架界面这样的医疗类样品等,制样时对样品厚度控制及表面质量均有一定要求。
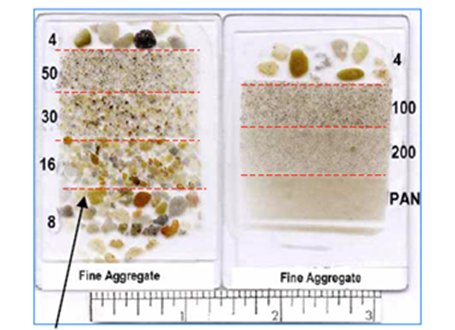
岩相薄片示例
单个样品的等间距分层制备
以微米级的层厚对样品进行连续精确切片(研磨/抛光)是大体积材料三维表征技术如3D-EDS,3D-EBSD分析中重要的样品制备方法,目前已经在先进材料研究领域中有所应用。效率、重复性及制样效果均是该类制样的考虑因素,一般建议采用智能化全自动磨抛设备进行,最小去除层厚可达500nm。

采用自动金相抛光连续切片原理(由QATM 全自动磨抛机系统实现)制样的3D-EBSD数据重构示例
总体说来,目标制备中,精度和效率是最为核心的因素。以往为稳妥起见,操作人员多采用手动制备方法,制样效果强烈地依赖于人的经验。随着现代制样技术的发展,金相设备的功能性、精确性及自动化程度都有大幅提升,将实验室人员从繁重的手动制样工作中解脱出来成为可能。
QATM针对目标制备的不同应用提供专业细分的解决方案。行业领先的Qcut 200A精密切割机,Saphir 550自动磨抛机及全自动磨抛系统Qpol 250 BOT 均配备定量磨削功能,为高精度、高重复性及高效率的目标金相制备提供了有力的支撑;同时,高品质的透明镶嵌材料设备及研磨抛光耗材也确保了制备目标可视性和稳定的材料去除率。
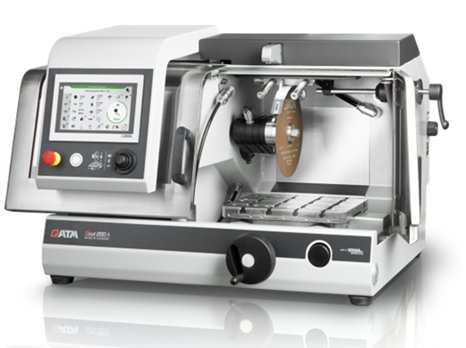


更多关于目标制备的技术细节,敬请期待。
